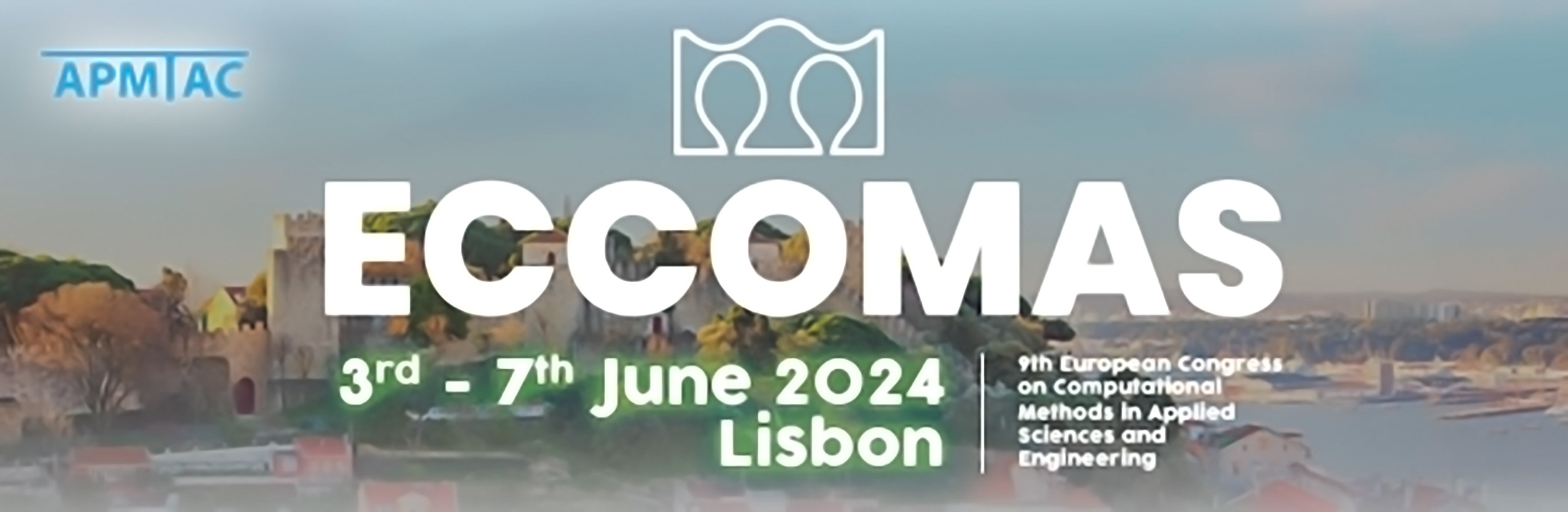
Numerical and analytical evaluation of resin flow during PCB pressing cycles
Please login to view abstract download link
This paper presents a comprehensive sequence of analytical methods for evaluating printed circuit board (PCB) pressing processes, augmented by numerical finite element (FE) simulations. The study considers the properties of the prepreg material, the structure of the PCB copper layer, and various pressing process parameters, all of which can be adjusted according to specific requirements. Our results are validated through experiments and compared with the established Squeeze Flow Model. The proposed methodology identifies potential weaknesses in the design of the copper layer, material selection, and pressing parameters prior to production. Additionally, the implementation of this methodology in an interactive user interface allows for rapid and efficient results, facilitating timely decision-making and process optimization.