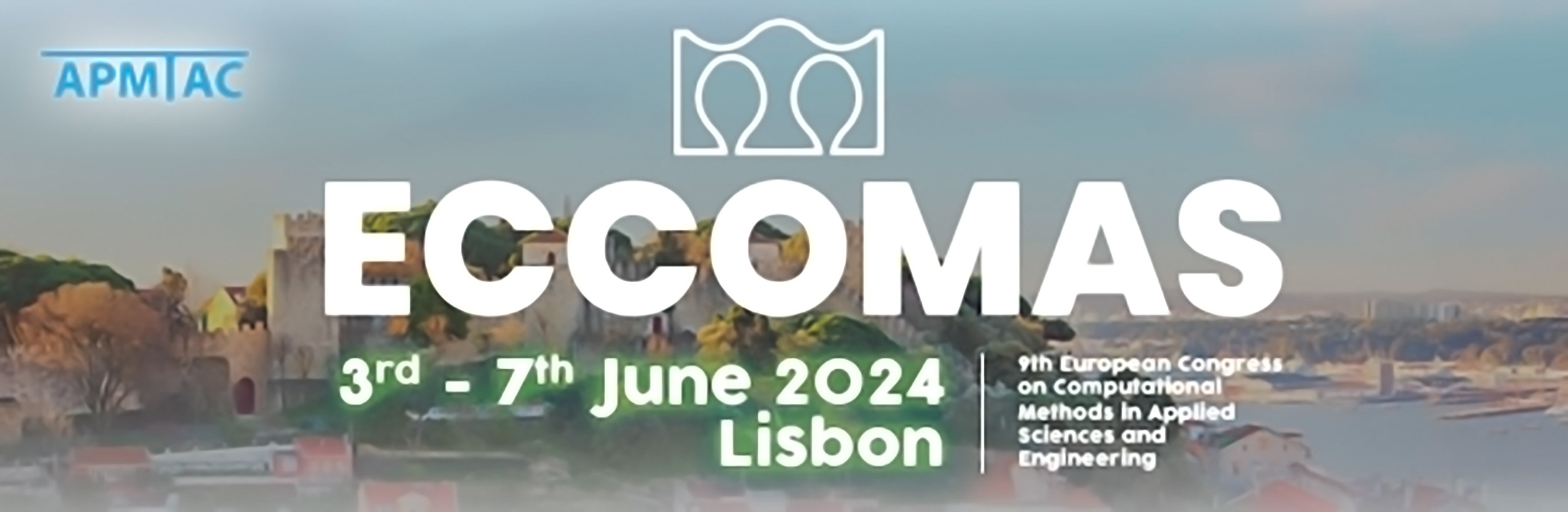
Mapping Manufacturing Variability to Composite Pressure Vessels’ Geometry
Please login to view abstract download link
In the context of vehicles powered by hydrogen fuel cells, hydrogen is stored as a compressed gas within tanks constructed from carbon fiber composites. These tanks are engineered with a margin of safety set at 2.25 times the nominal working pressure [1]. Showing a minimal variability in the tank's strength will allow for a decrease in this margin of safety. This can be accomplished by predicting both the vessel's strength and its associated uncertainties. In this work, several composite pressure vessels (CPV) were manufactured through fiber winding, and the parameters that control the winding were recorded as time signals. Some of these parameters include used fiber length, fiber tension, winding speed, liner pressure and fiber volume fraction. The winding process is controlled by an algorithm that follows winding paths based on a defined winding angle and number of circuits around the vessel. These paths are defined by Euclidean and cylindrical coordinates that can be used to calculate the amount of fiber used between each coordinate. This obtained fiber used is then matched to the fiber used signal recorded during winding in order to match the recorded signals to the winding paths. This allows the parameters to be mapped to the geometry of the vessel. Afterwards, Gaussian Process Regression (Kriging) is used to obtain random fields over the geometry of the vessel for each manufacturing parameter of interest. This allows to identify and visualize the distribution of these parameters over the geometry of the vessel and potentially identify areas of the vessel where failure is more likely to start.