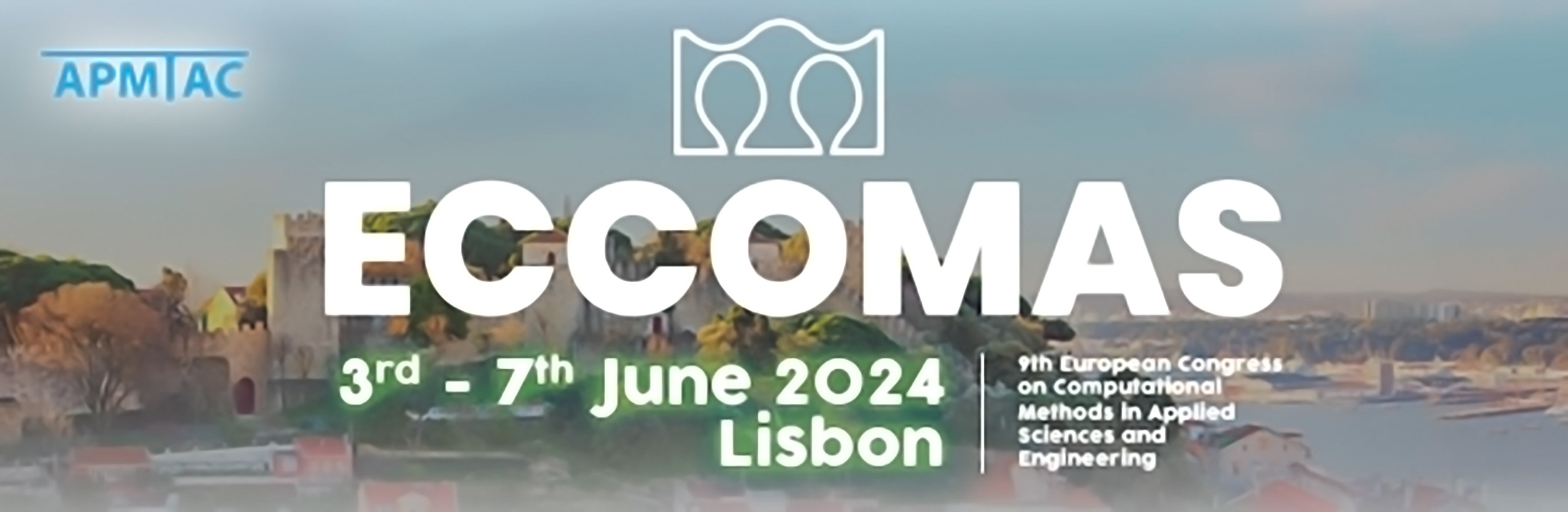
Numerical Based Optimisation of Preheating and Powder Sintering in Electron Beam Powder Bed Fusion
Please login to view abstract download link
Powder bed fusion deploying the electron beam (PBF-EB) is characterised by its high power, which can reach up to 45 kW in current systems. In combination with the capability to deflect the electron beam at very high velocities (up to 10,000 m/s), the electron beam can operate as a general heating source and enable ambient process temperatures in the range of 1,000 °C. This high-temperature environment facilitates the defect-free processing of crack-sensitive alloys e.g. Ni-base superalloys and TiAl. The separate heating step to maintain these high operating temperatures is inherent to the PBF-EB process itself. As sintering during this so-called preheating is essential to achieve a certain degree of mechanical stability in the powder bed, preventing repulsion of the powder particles due to the imposed charge (smoke) during the melting process. [1] The aim of this study is to investigate the impact of the conventional preheating scheme on the temperature and sintering distribution of the powder bed. Therefore, a finite difference-based model was implemented, capable of depicting the thermal evolution during scan-wise preheating. In combination with the utilization of a powerful GPU parallelisation at a high-performance computing (HPC) environment, this numerical tool enables the efficient investigation of the heat flow at macroscopic scale. Additionally, by including a relationship between the thermal history and the sintering behaviour, a quantitative measure for the degree of sintering can be derived from the model. Simulation of a regular Ti64 build reveals that differing properties between consolidated and powder regions create inhomogeneous sinter and thermal distributions, which can also be observed experimentally. Consequently, a new optimisation-based strategy is proposed. The strategy adapts the energy input locally to maintain a constant temperature field while achieving a higher sintering degree above consolidated material, forming the basis for improved melting results. REFERENCES [1] C. Körner, Additive manufacturing of metallic components by selective electron beam melting — a review, International Materials Reviews, Vol. 61, pp. 361–377, 2016.