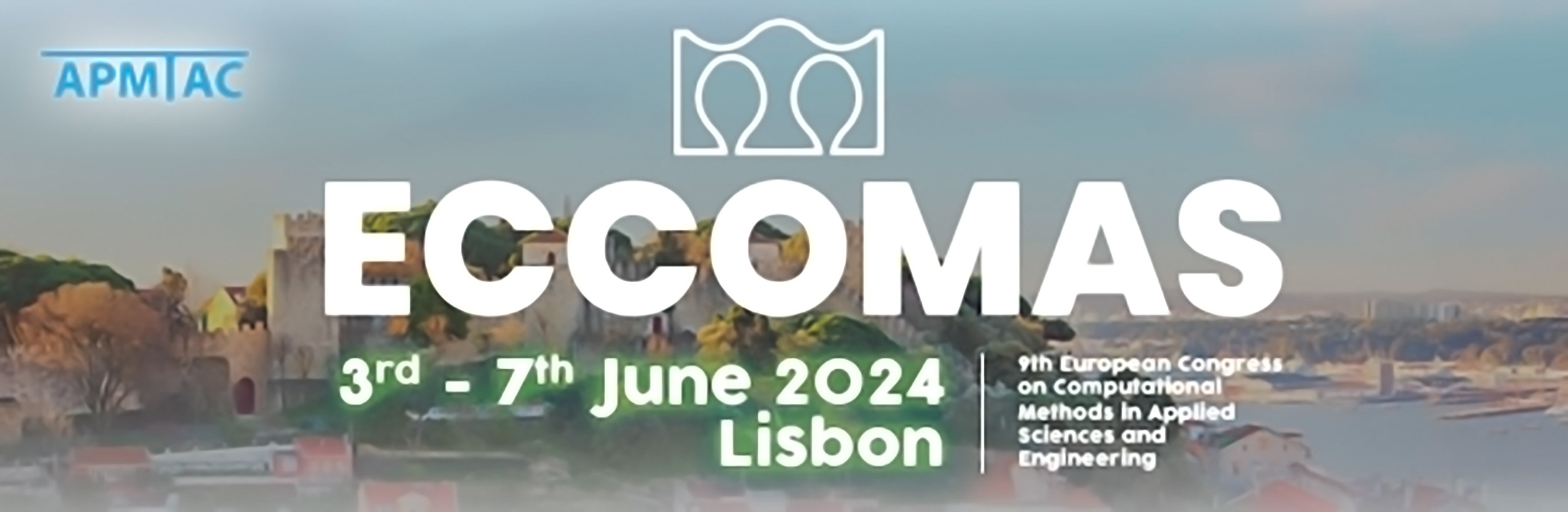
Investigation of Glass above the Glass Transition Temperature by means of a Thermo-Mechanically Coupled Material Model
Please login to view abstract download link
Thin glass products find applications in various engineering fields such as electronics, medical equipment, and automobiles. To achieve cost-effective production of highly accurate and complex surface shapes, a new glass processing technique called non-isothermal glass molding has been developed (see [1]). However, the production of thin glass components using this technology still faces challenges such as shape distortions, cracks, and surface defects. To address these issues, experimental investigations and mechanical modeling of glass above the glass transition temperature are combined to simulate the glass-forming processes. Previous experiments have shown that the material behavior can be suitably predicted using the Maxwell model (see e.g. [2]). The used viscoelastic formulation based on [3] allows for the thermo-mechanically consistent description of the material, taking into account the observed rheological effects and large deformations. The relaxation behavior is described using a stress-dependent relaxation time, and the dissipation generated is also considered. Isothermal uniaxial compression tests are conducted at different strain rates and temperatures to gather experimental data. By combining these experimental results with simulations, a multi-curve-fitting approach is employed to determine suitable material parameters for specific temperatures. [1] A.-T. Vu, H. Kreilkamp, O. Dambon, and F. Klocke, Nonisothermal glass molding for the cost-efficient production of precision freeform optics. Optical Engineering 55(7), 071207 (2016). [2] T. Zhou, J. Yan, J. Masuda, and T. Kuriyagawa, Investigation on the viscoelasticity of optical glass in ultraprecision lens molding process. Journal of Materials Processing Technology 209(9), 4484-4489 (2009) [3] S. Reese and S. Govindjee, A theory of finite viscoelasticity and numerical aspects. International Journal of Solids and Structures 35(26-27), 3455-3482 (1998)