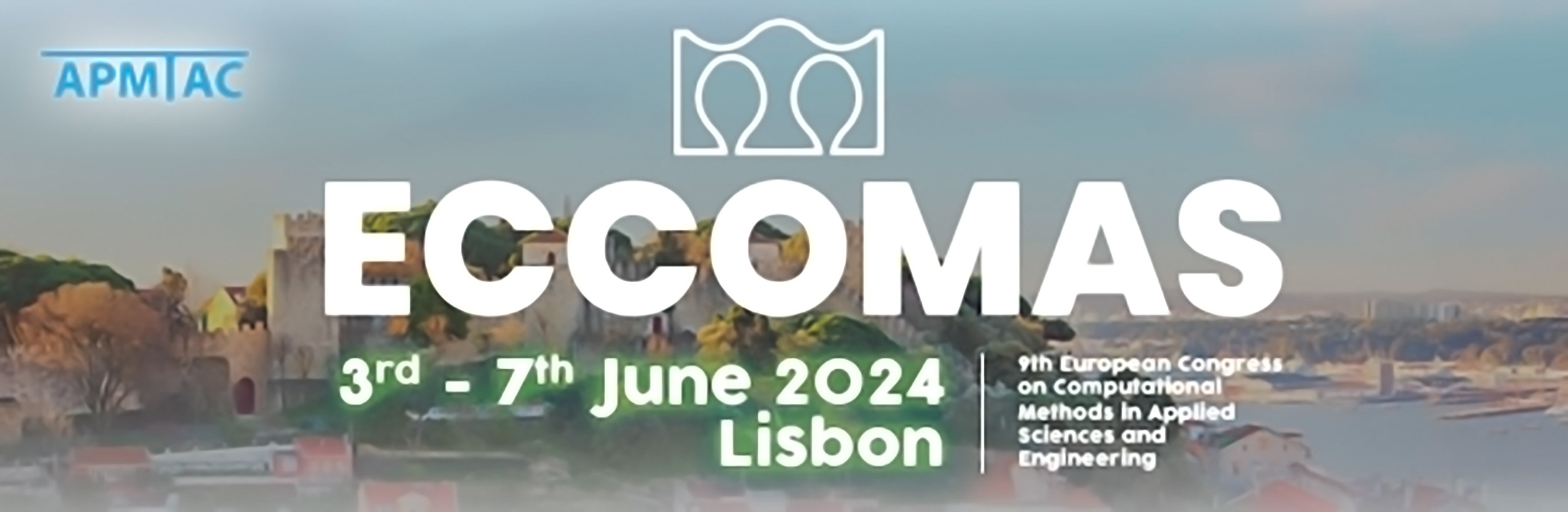
Least-weight design of variable stiffness composites considering manufacturing signature and unified structural theories
Please login to view abstract download link
Modern aircraft structural design has favored composite materials over the last few decades. This change can mainly be attributed to the increased strength-to-weight ratio offered by composites compared to standard metallic alloys. Automatic fiber placement (AFP) has made it possible to vary the orientation of the fibers in space, thus improving mechanical performance to an even greater extent. Variable Angle Tow (VAT) or Variable Stiffness Composites (VSC) have been developed to enhance structural performance through material optimization and effective load-bearing configurations. The use of these materials is essential to ensure optimal results and further decrease the weight of aircraft and aerospace structures. Unfortunately, defects such as gaps and overlaps could arise during the manufacturing process. Whereas the latter increases local thickness, the former causes resin-rich areas within each lamina. This study directly combines the Carrera Unified Formulation (CUF) and the Defect Layer Method (DLM) into the optimization process to achieve an efficient and affordable framework for modeling VSC's structural behavior and manufacturing process. A mixed-integer optimization strategy is specifically designed to select the least-weight design of a VAT laminate while also fulfilling first natural frequency and buckling performances. The research has two main aims: to determine the minimum number of layers required to satisfy the fundamental frequency and buckling constraints, accounting for the manufacturing signature, and (ii) to investigate how the selection of the structural theory influences the optimal solutions.