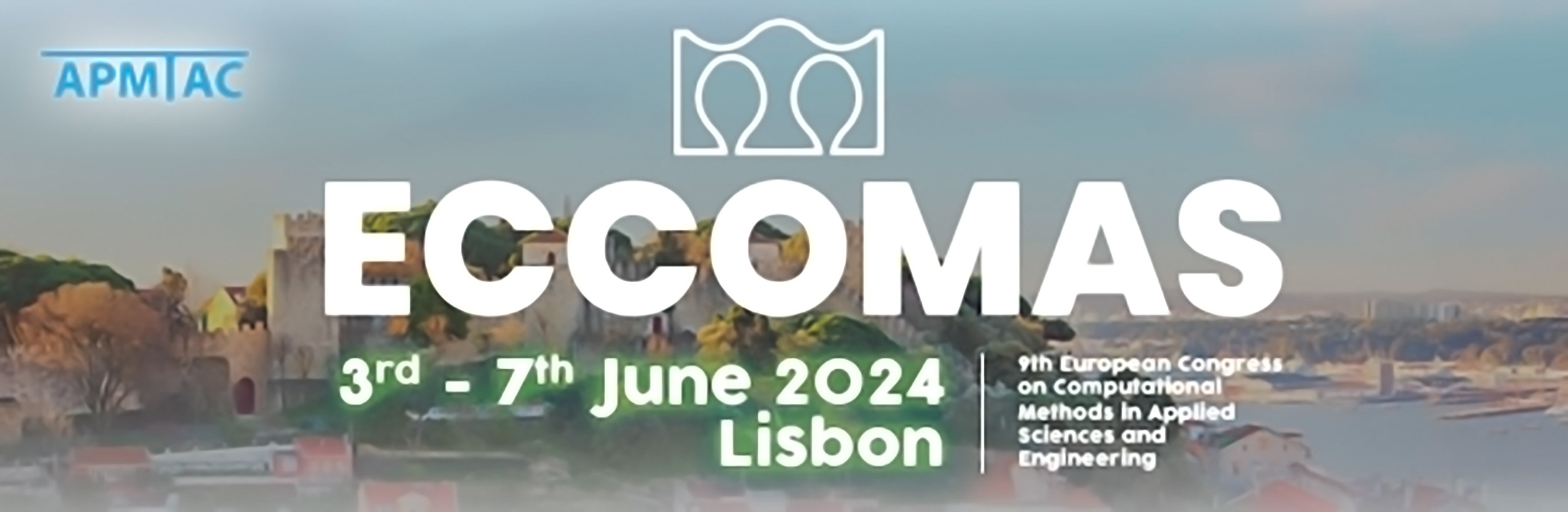
Micro-scale analysis of rough surfaces using non-conforming meshes
Please login to view abstract download link
Contact problems are known for their high level of complexity, even when avoiding lubricated conditions. The behaviour of the contacting surfaces is dictated by parameters such as the elastoplastic properties of both solid surfaces and their surface characteristics, such as roughness or chemical bonding. Solid lubricants, which are materials that, despite being in the solid phase, can reduce friction between two surfaces sliding against each other, without the need for a liquid lubricant. In that case, during sliding contact, structural transformations and/or chemical reactions occurs, which generate locally a tribolayer (tribological layer) with low friction properties [1]. They are known as self-adaptive low friction coatings. Unfortunately, tribological tests indicate that the formation of the tribolayer is very sensitive to the sliding contact conditions, contributing to inconsistent results in industrial applications. Numerical models at the micro-scale can be used to try to improve the understanding about the conditions for the formation of the tribolayer, combined with an experimental approach. In this context, this work presents a preliminary work that focuses on evaluating the potential of using non-conforming meshes for the analysis of contact problems for rough surfaces, to reduce the computational time. The finite element model was built in DD3IMP finite element code [2]. The results show that the model can capture the main effects of the bulk material constitutive behaviour, which is known to have a significant impact on the problem, as well on local changes on the friction conditions. [1] Yaqub, T. Bin, Bruyere, S., Pierson, J. F., Vuchkov, T., and Cavaleiro, A. 2020, “Insights into the Wear Track Evolution with Sliding Cycles of Carbon-Alloyed Transition Metal Dichalcogenide Coatings,” Surf Coat Technol, 403, p. 126360. https://doi.org/10.1016/J.SURFCOAT.2020.126360 [2] Menezes, L.F., Teodosiu, C. 2000, “Three-dimensional numerical simulation of the deep-drawing process using solid finite elements”, J Mater Process Technology, 97(1-3), p. 100–106. https://doi.org/10.1016/S0924-0136(99)00345-3