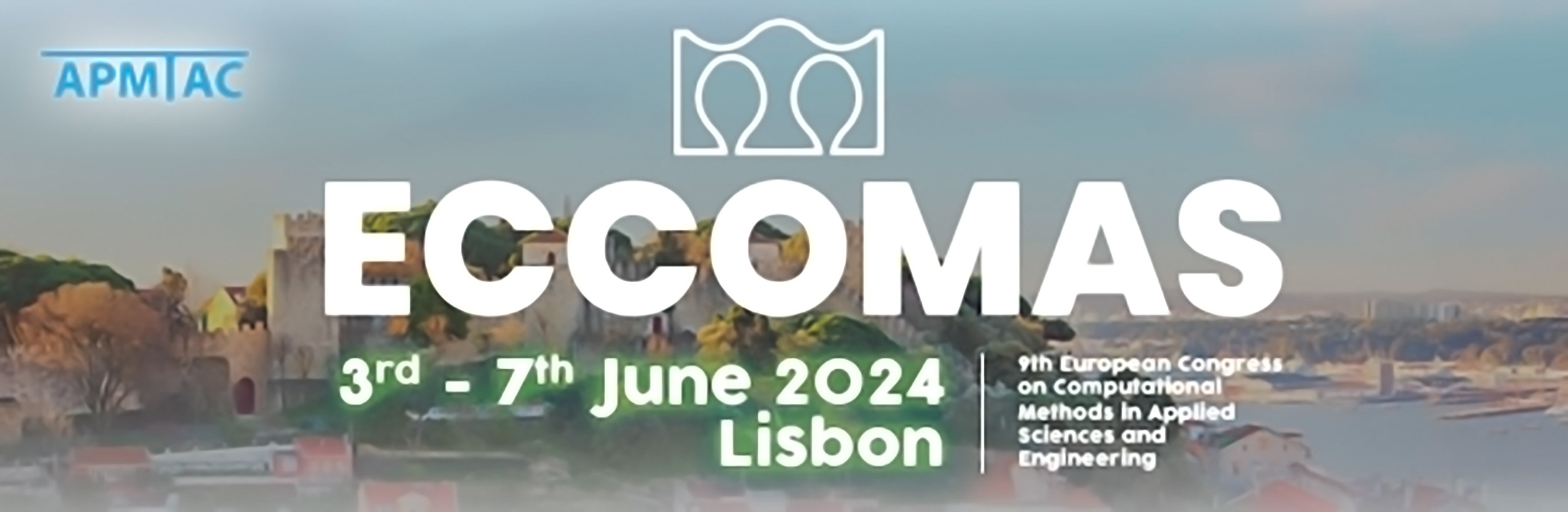
AI-Driven Stress Analysis in Varied Fiber Geometries of Particulate Polymer Composites
Please login to view abstract download link
Particulate polymer composites (PPC) are crucial in engineering due to their distinctive properties. Incorporating particulate fillers enhances mechanical properties, enabling engineers to customize material design for specific applications and offering flexibility in manufacturing components across various industries. Hence, the significance of PPC emphasizes the need for thorough studies on their mechanical behavior. In recent engineering practice, Artificial Intelligence (AI) has become a valuable tool for tackling various challenges, including the evaluation of materials such as PPC. While Finite Element Modelling remains a prevalent method for studying the mechanical behavior of PPC, AI may provide a viable means of predicting the mechanical response of the PPC materials and overcoming simulation runtime constraints. Subsequently, instead of relying on time-intensive laboratory experiments to optimize material and position combinations for peak mechanical performance, AI offers an efficient means to observe and analyze the mechanical response. Its role in analyzing stress patterns within PPC, corresponding to fibers oriented in different positions and orientations within neat epoxy, provides critical insights into the overall stresses exhibited by the polymer composite. In extending the application of AI to predict PPC material responses, we have employed a paired image-to-image (Pix2Pix) algorithm that excels in qualitative analysis, proficiently capturing and replicating stress patterns. In contrast to existing literature, our model is trained on a labeled dataset comprising the PPC mechanical properties and ABAQUS-derived image frames depicting evolving stresses. The model generates principal stress patterns across the Representative Area Element (RAE) of experimentally tested specimens. Notably, the Pix2Pix algorithm has shown a high correlation (0.997 for carbon fibers, 0.947 for epoxy) in predicting major principal stresses. This demonstrates that the AI model offers engineers advanced predictive capabilities, improved stress insights, efficient material characterization, potential time and cost savings, and a broader understanding for making informed design decisions.