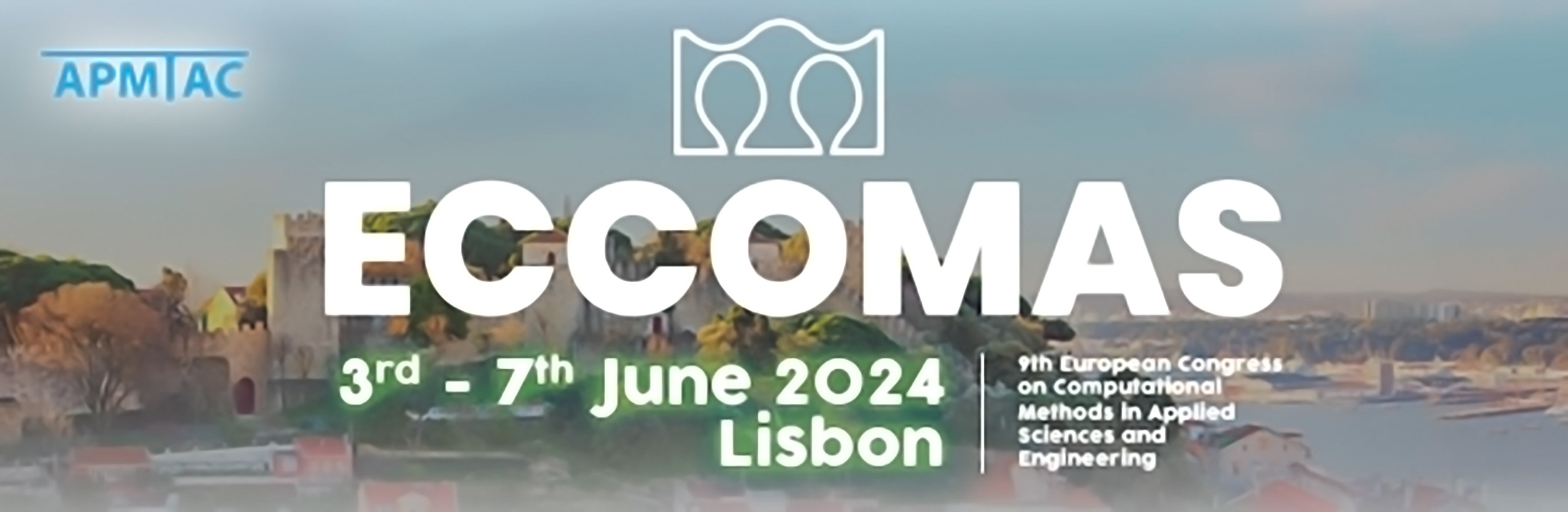
HAWT Efficiency Increase via Active Flow Control Implementation
Please login to view abstract download link
In this research, we conducted a comprehensive Computational Fluid Dynamics (CFD) investigation on the DTU-10MW reference blade wind turbine [1], employing the Unsteady Reynolds-Averaged Navier-Stokes (URANS) K − ω SST turbulence model. In general, there is a lack of experimental data for large horizontal axis wind turbines (HAWT), and most of the existing studies have predominantly relied on potential-flow methods, Blade Element Momentum (BEM) methods, and vortex methods[2]. These approaches fail to provide a good understanding of the boundary layer (BL) dynamics around the turbine blades, particularly in pinpointing separation points. Our study addresses this gap by performing a series of 2D simulations on 24 sections cut along the turbine blade. This allows us to identify for each section, the BL thickness and its time-averaged separation point, the dynamic lift and drag coefficients, and its associated oscillation amplitude. The vortex shedding frequency, pressure, and skin friction coefficients were as well obtained for each section. Some of the results for a wind speed of 10m/s are presented in figure 1, where the BL time-averaged separation point, its associated frequency, the lift coefficient, and its peak-to-peak amplitude are introduced as a function of the blade non-dimensional radius. A good agreement is observed with the previous research undertaken by [3]. This initial information is needed to implement the Active Flow Control (AFC) technology in the sections where BL separation exists. After optimizing the AFC parameters and when employing Synthetic Jets (SJ) on the blade section z/R = 0.35, the resulting CFD simulation shows that the boundary layer was almost fully reattached, this can be seen in figure 2 where the streamlines on the upper airfoil surface for the baseline case and the AFC one are presented. In order to evaluate the WT efficiency increase, the AFC implementation in the section studied was energy assessed, it was obtained that the SJ-AFC system consumed only 6.4% of the increase of energy generated by the wind turbine, therefore highlighting the potential of AFC techniques to enhance HAWT’s efficiency.