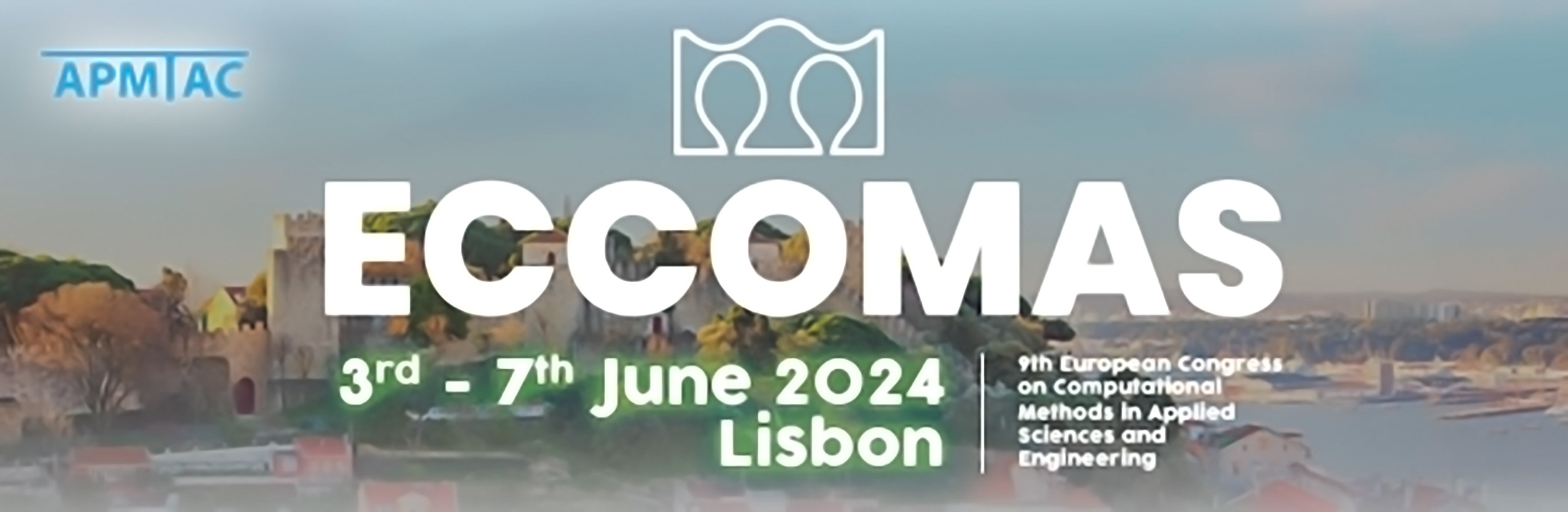
DuoDIC and MultiDIC: Open-Source Software for 3D Digital Image Correlation and their Applications in Solid Mechanics
Please login to view abstract download link
3D Digital Image Correlation (3D-DIC) is an optical-numerical non-contact technique for measuring the 3D shape and full-field displacement, deformation, and strain from stereo images of an object’s surface captured from multiple views. It is frequently used in various mechanical applications, such as characterizing material properties, identifying structural damage, and validating numerical simulations. However, commercial 3D-DIC packages are expensive and usually proprietary and closed-source, posing a barrier, especially for students and researchers. We have recently released two open-source 3D-DIC software written as MATLAB toolboxes [2, 3]. MultiDIC is designed for multi-view applications, allowing instantaneous calibration of numerous cameras using a dedicated 3D calibration object [2]. DuoDIC works only with two cameras, but offers a simpler calibration procedure, requiring a flat calibration target [3]. The 3D-DIC procedure in both packages is organized into four main steps: (1) stereo camera calibration: computing extrinsic and intrinsic parameters from a calibration image set. (2) 2D-DIC: identifying grids of matching points using spatial and temporal cross-correlation. (3) 3D reconstruction: combining the results of steps 1 and 2 to reconstruct image points in 3D space. (4) post-processing: deriving full-field displacement and strain maps from the 3D points. We experimentally and numerically validated the displacement and strain results, and demonstrated the ability of a 360-deg MultiDIC setup to reconstruct 3D surfaces from multiple cameras with little merging errors. Since their publication, the two software have been utilized by other research groups in a wide range of mechanical applications, including biomechanics of tissues and body parts, medical device testing, characterization of composite materials, identifying cracks and fractures, imaging traction stresses, evaluating the performance of various sensors, and more.