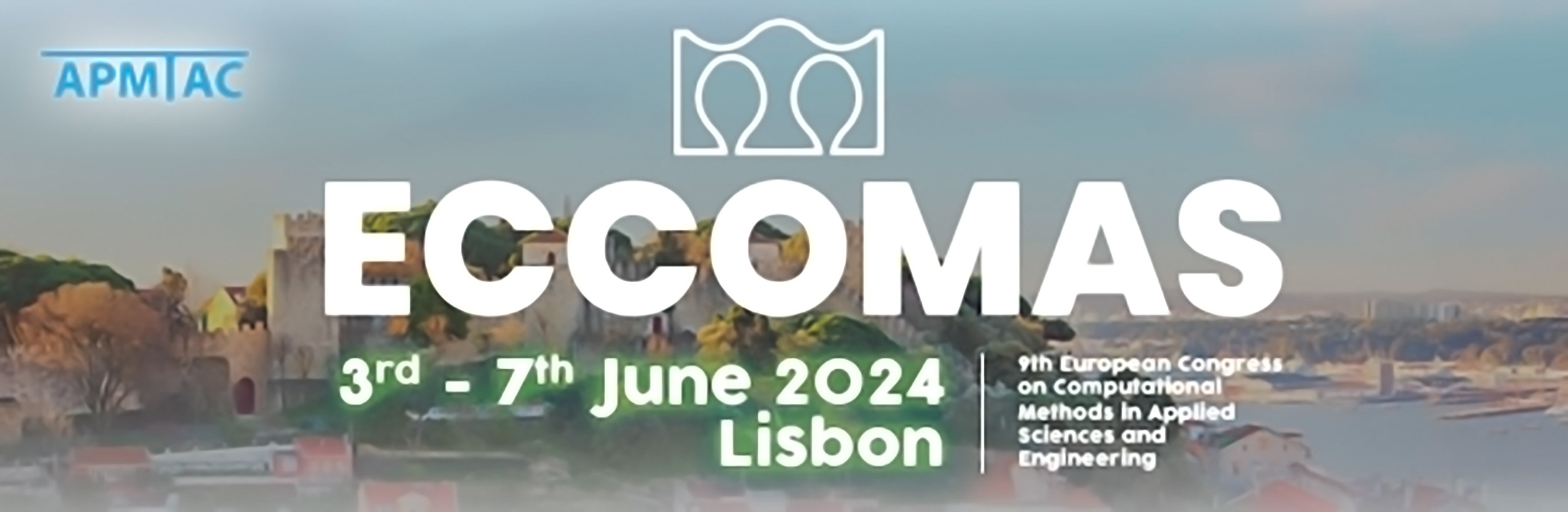
A Virtual Environment Based on the Frenet Frame for Manufacturing Variable Angle Tow Composite Structures with LATP
Please login to view abstract download link
The development of cutting-edge manufacturing techniques has sparked a revolution in the aerospace industry. Among them, laser-assisted automated fibre placement (LATP) allows the production of components through in-situ consolidation of fibre-reinforced thermoplastic composite materials, resulting in high-quality parts without the need for a secondary consolidation processing step [1]. This advancement has facilitated the optimisation of fibre-reinforced composite laminates through the application of variable angle tow (VAT) design strategies, significantly enhancing structural performance by positioning steering fibres aligned to preferred load paths [2]. In this context, this work aims to present a novel approach to manufacturing VAT composite structures via LATP using a virtual environment implemented in Matlab. The robot's steering movements are planned and executed through a series of interpolated short paths and linear commands, executed within a virtual environment in Matlab, employing local coordinates and the differential geometry of the Frenet frame. To achieve this objective, four integrated modules were developed, allowing the user control over the input parameters of the robot's actuators, the structure's geometry, the visualisation of the steering planning, and the generation of the manufacturing code. Hence, the potential and limitations of the methodology were assessed by continuous tow steering around an elliptical cutout of a composite panel [3].