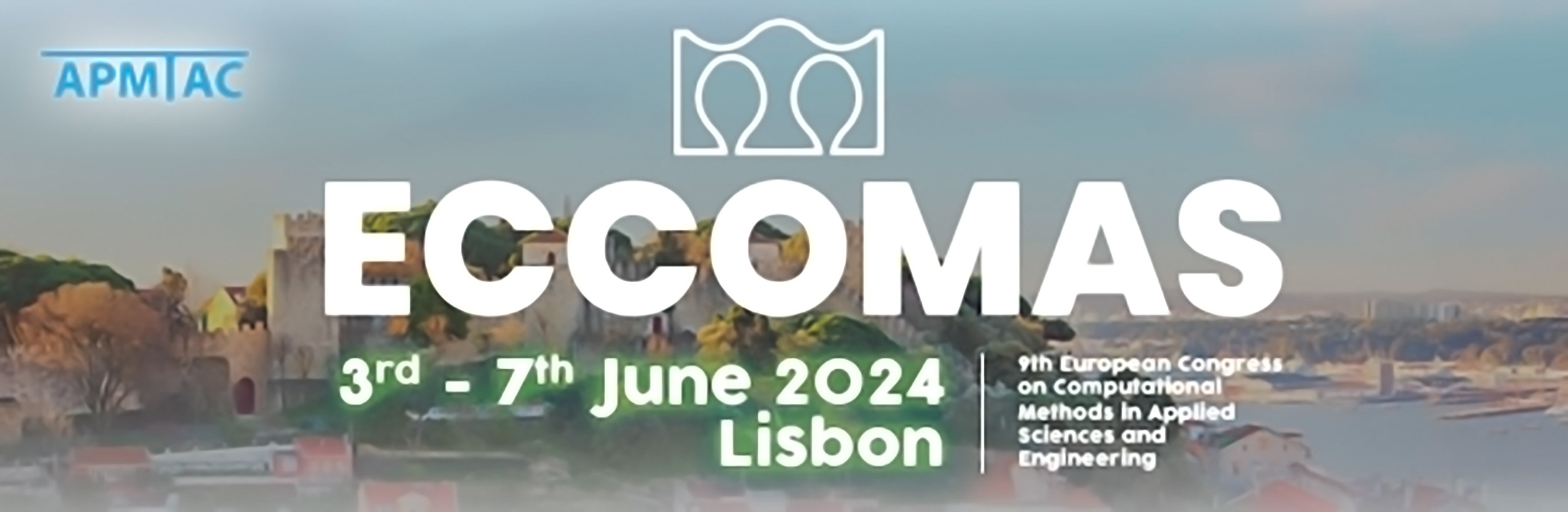
Multidisciplinary Optimisation of Additive Manufactured Heat Exchangers for Aeronautical Applications
Please login to view abstract download link
Topology Optimization (TO) aims to determine location, shape, and connectivity of voids within a solid design space to maximize the value of an objective function, under specified constraints. In the context of heat exchangers, TO offers enhanced design flexibility compared to conventional shape optimization, yielding improved performance and reduced weight. Additive Manufacturing (AM) emerges as a versatile solution for crafting intricate geometries resulting from TO, overcoming the limitations of traditional manufacturing processes. The objective of this research is to establish a proof-of-concept workflow for the multiscale optimization of additive manufactured Micro-Channel Heat Exchangers (MCHX) based on lattice-like structures. The envisioned application is a cutting-edge cooling system for power electronic, where MCHX serves as a pivotal component for managing the working temperature of batteries, fuel cells, and preventing overheating of electronic equipment. TO of MCHX is intrinsically a multi-scale problem, where performances of the MCHX are strongly influenced by the flow regime at the scale of micro-channels, [2]. To address this, homogenization theory is employed, treating the lattice matrix as an equivalent porous medium at the macroscale. A Machine Learning (ML) model, trained offline with data from Direct Numerical Simulations (DNS) provides closure relationships to incorporate micro-scale effects at the macroscale. The ML model is based on a multi-fidelity approach, where few high-fidelity simulations are used in conjunction with many low-fidelity computations to infer such relationships. CFD simulations at the micro-scale are performed in OpenFOAM, while Immerflow (Optimad) has been employed for macroscale simulations. The optimization process is managed by modeFRONTIER. Numerical results obtained with this methodology are compared against experiments performed on the whole heat-exchanger by Rolls-Royce.