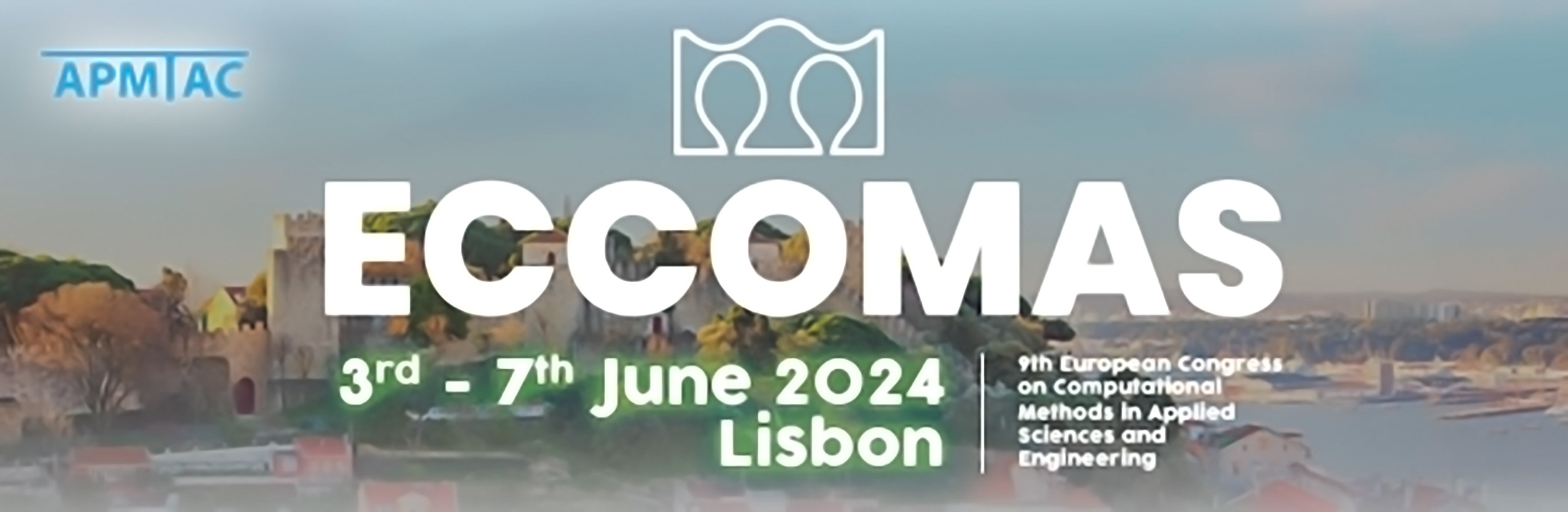
Multi-phase-field lattice Boltzmann modeling of thermal fluid flow and microstructural evolution in powder bed fusion
Please login to view abstract download link
Powder bed fusion (PBF) is typically used in metal additive manufacturing (AM). In PBF, complex physical phenomena such as laser irradiation of powder particles and substrates, melting and solidification, liquid phase flow in the molten pool, and polycrystalline grain growth following solidification occur simultaneously. Because the properties of metal AM products are determined by the solidification structures and internal defects, predicting their formation processes with high accuracy is essential. The solidification structures and internal defects are strongly affected by the liquid phase flow in the molten pool. Therefore, a model that can simultaneously reproduce the liquid phase flow and solidification structural development is required. Only few previous studies have simultaneously focused on both liquid flow and material microstructures. In addition, different interface tracking models have been used for liquid phase flow and microstructural evolution, which are not necessarily accurate. Moreover, high computational costs represent a major issue in these simulations. In this study, we develop a phase-field model to express simultaneously the liquid phase flow and solidification structural evolution that occur during the PBF process. In the developed model, all boundaries, including grain boundaries and solid–liquid and gas–liquid interfaces, are represented using multi-phase-field (MPF) variables. The liquid phase flow in the molten pool is solved using the lattice Boltzmann method, where the gas–liquid interface is treated as the free surface. Material microstructural evolution is also represented using the MPF method. As the temperature gradient in PBF is significantly high, MPF simulations require small grids. Therefore, multiple GPU parallel computing is implemented to speed up the three-dimensional simulations.