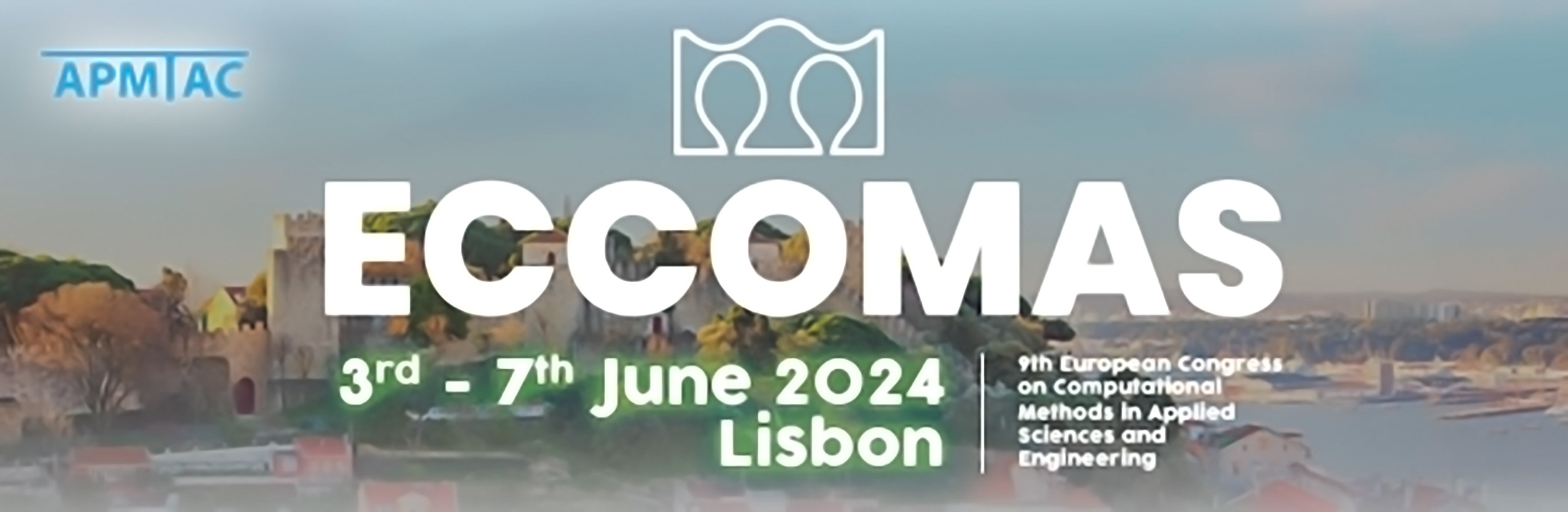
Combined Optimisation of the Layout and Topology of Stiffeners for Thin-Walled Structures using FE-Based Parameterisations
Please login to view abstract download link
Because of properties such as being lightweight, having the ability to span large surface areas and being highly effective at carrying loads, thin-walled or shell structures are found in a wide range of engineering applications. Despite its many advantages, the performance of a thin-walled structure is often hindered by drawbacks such as susceptibility to buckling and vibrations. Fortunately, its behaviour can be improved (while also retaining its superior strength-to-weight ratios) through the addition of stiffeners. Here we present a simple two-stage framework to optimise both the stiffener arrangement and the topology of the individual stiffeners. In the first stage, a ground structure is generated by adding beam elements to the finite element mesh of the thin-walled structure in a predefined pattern. To determine the location of the stiffeners that will optimise some performance criteria, a topology optimisation problem is solved during which the cross-sectional areas of the beam elements are used as the topology design variables. Typically the predefined layout of stiffeners remains fixed during the optimisation process [1]. Instead, we allow the pattern to adapt by simultaneously applying node-based shape optimisation [2] to find the optimal in-plane node positions. In the second stage, an extrusion step is performed at the optimised stiffener locations. The extruded ribs form the design space for a new structural optimisation problem used to determine the optimised topology or shape of the individual stiffeners. We apply the proposed method to several examples from the aerospace and automotive industries. We show that this method can be used to improve performance objectives such as compliance and stability while also satisfying weight or volume constraints.