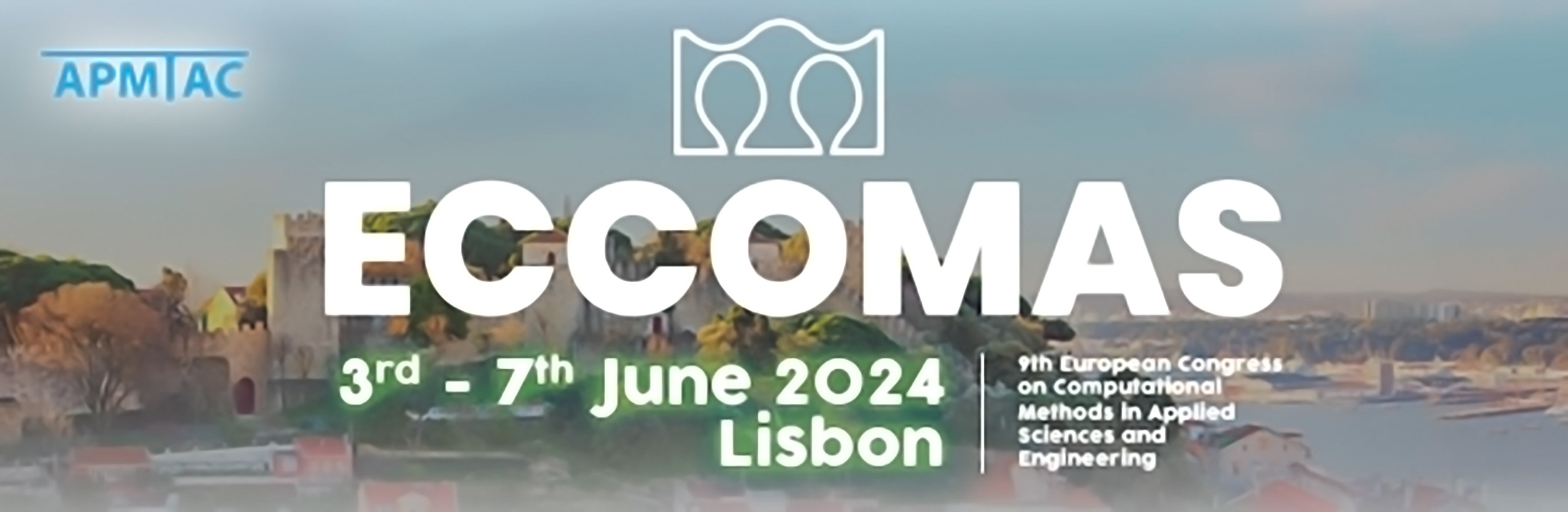
On the time-dependent material properties during material extrusion (MEX) process simulation using orientation tensors
Please login to view abstract download link
Process-related distortion and residual stresses are among the major challenges in manufacturing components using material extrusion (MEX). This is due to the wide range of possible material properties resulting from the different possible deposition strategies. The numerical prediction of these resulting process-related component properties is a promising tool to replace complex experimental investigations. However, the small dimensions of the separated strands compared to the component size lead to unfeasible computational effort if each strand is modelled individually. To improve the computational efficiency of finite element MEX process simulations, several filament strands have to be combined in one element. These larger elements are no longer orthotropic, but can exhibit any anisotropic material orientation. One way to describe the resulting material orientations are orientation tensors of 2nd and 4th order [1]. In our previous work, we have presented a method to determine time-dependent orientation tensors from a given G-code during process simulation for an element [2]. Based on the present methodology, this work investigates the resulting anisotropic material properties in the prediction of temperature distribution and distortion behavior. For this purpose orientation averaging based on measured orthotropic material properties and time-dependent orientation tensors are used. The influence of the element size on the local material orientation and the resulting influence on the distortion prediction are discussed. The work shows that an unlimited number of effective material properties can occur within a finite element during the process time, even when the infill orientation is constant. This is caused by the differently varying material properties of the neighboring strands and it underscores the need for such homogenization methods.