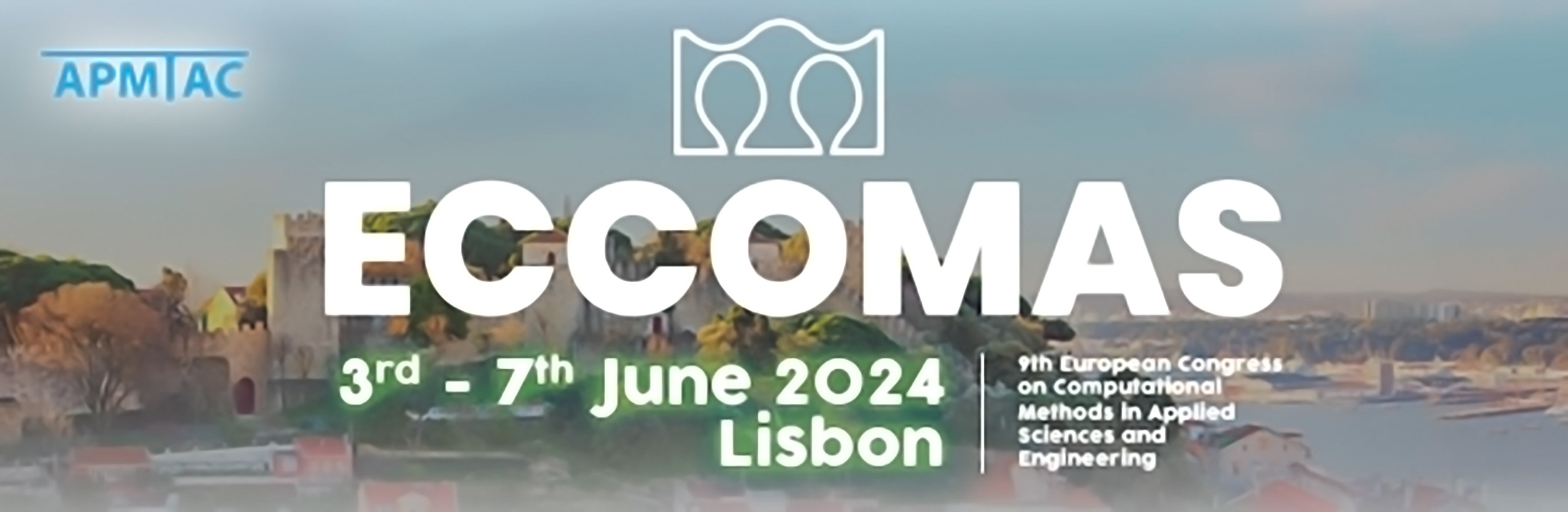
Application of NURBS-based Metamodel to Fused Deposition Modeling 3D Printing Process
Please login to view abstract download link
Fused Deposition Modleing (FDM) is a cost-effective and versatile additive manufacturing method widely used due to its easy integration in design processes [1]. Several process parameters and printing strategies significantly impact the quality of FDM-printed parts, prompting investigation of a broad design space to improve accuracy, mechanical properties, and process efficiency. Due to the thermomechanical nature of the printing process, the combination of temperature gradient and printing strategy can create distortions (warpage) in the printed part. This work proposes a numerical strategy to perform a gradient-based optimisation of the most relevant parameters of the FDM process, for Acrylonitrile Butadiene Styrene (ABS) filament, by means of metamodel obtained by Non Uniform Rational Basis Splines (NURBS) [3]. Firstly, a parametrised 3D thermomechanical finite element (FE) model is created using a SparseGrid-based method [2] to simulate post-cooling residual deformation. Subsequently, a NURBS-based metamodel is trained and validated to predict the influence of the process parameters on the warping phenomenon. Finally, the process parameters are optimised by means of a gradient based algorithm in order to minimise the warpage effects while considering volumetric speed constraints.