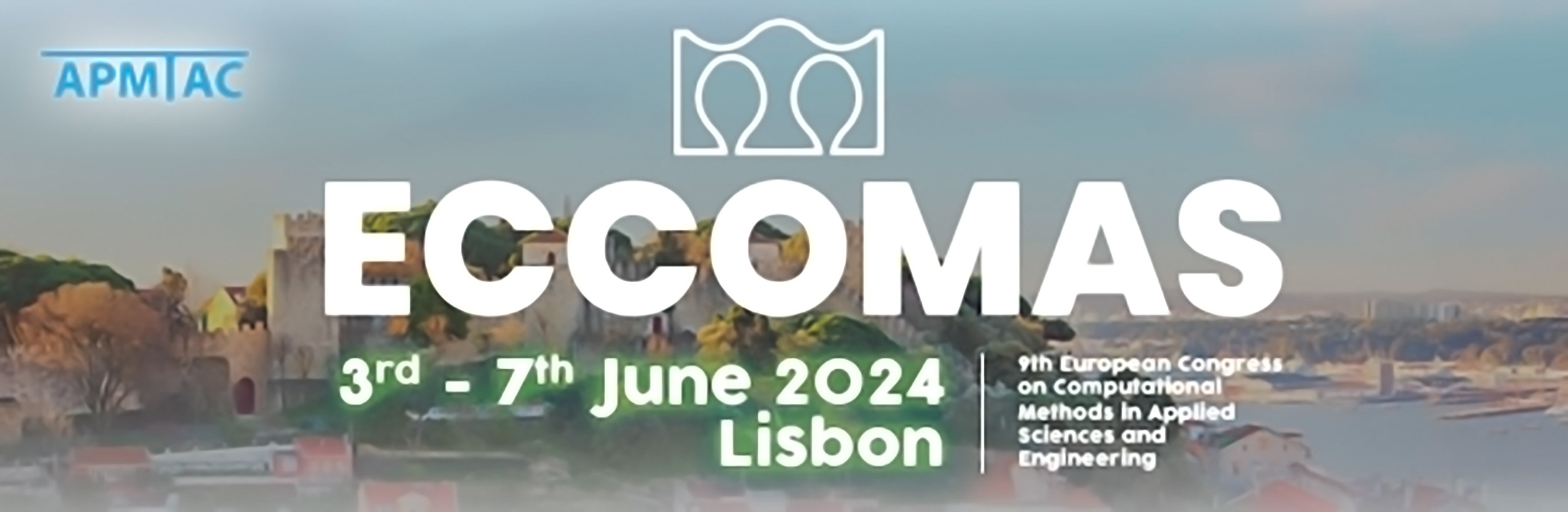
Phase-field ductile fracture simulations of thermal cracking in additive manufacturing
Please login to view abstract download link
In this contribution, we present a computational framework to simulate thermo-ductile fracture in thermo-elasto-plastic solids undergoing finite deformation, and apply it to predict hot cracking phenomenon during metal additive manufacturing process. To this end, a phase-field thermo-ductile fracture model is derived in a thermodynamically consistent manner, with the intercoupling mechanisms between elastoplasticity, phase-field crack and heat transfer comprehensively considered, extended from our previous work \cite{ruan2022}. Notably, the coupling of damage-plasticity is threefold, which exhibits in the degradation function, the yielding surface and the fracture toughness, respectively. The proposed fracture model is validated with whole ductile process encompassing elasoplasticity, hardening, necking, crack initiation and propagation. The model is further employed to simulate hot cracking phenomenon in additive manufacturing, specifically combined with the phenomenological model and non-isothermal phase-field model for laser powder bed fusion process \cite{yang2023elasto}, sequentially. Thereby not only the thermal strain but also the solidification shrinkage is included to calculate thermal stress. The study shows that the proposed model and simulation scheme is capable of predicting hot cracking in additive manufacturing process.