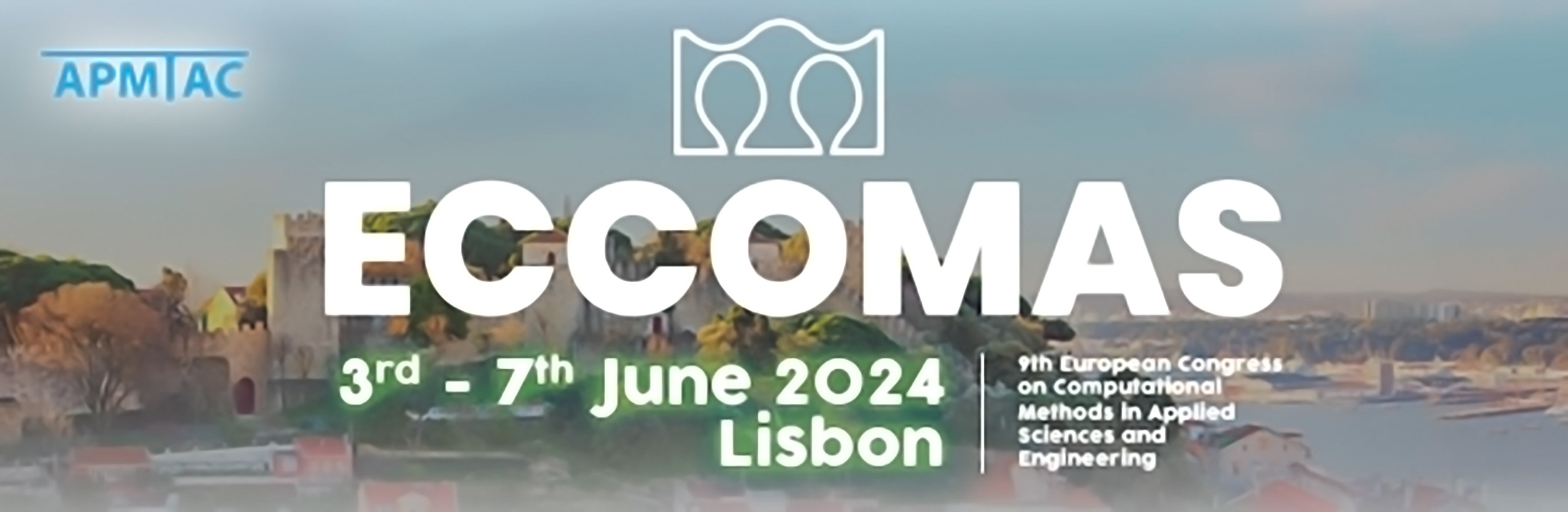
Optimization of a Roller Pump Using a 2D Numerical Simulation Model
Please login to view abstract download link
Roller pumps are used in the delivery of cell suspensions or as circulatory assist devices, but the shear stresses inside the pump can contribute to undesirable cell damage, called hemolysis. To better understand the mechanisms inside the tubing, which are not optically accessible, the internal flows in a roller pump are investigated numerically. In recent years, several numerical models for roller pumps have been developed, ranging from two-dimensional setups that account for tube movement by either loading a pre-set geometry or generating the geometry in a two-dimensional analytical model, to complex three-dimensional models that incorporate fluid-structure interaction calculating the mechanical deformation of the tubing and the mutual interaction of the solid and fluid materials. Most of these models have in common that they work with a strongly under-occluded tube, with the degree of occlusion varying between 50 \% and 90 \%. Models with an under-occlusion of the tube lumen tend to underestimate both flow transport and the resulting shear stresses. Using the open-source CFD software OpenFOAM, the 2D fluid mechanics model by Zhou et al. \cite{ref-zhou2014} is extended to allow for varying the occlusion and several pump parameters to find a low-shear transport setting. The parameters subject to variation include the occlusion, the number of rollers, rotational speed, fluid viscosity and tube diameter. The presented model enables the investigation of fluid flow within a roller pump under very small gap widths. An occlusion of 98.4 \% is investigated. During the evaluation of the simulation data, an analysis of fluid shear stresses, flow velocity and pressure fields is conducted. The findings show that optimization of shear stress and the flow rate can achieved by selecting the right under-occluded pump setting and using tubing of maximum possible diameter, minimizing the occurring shear stresses. The results are to be incorporated into a 3D model, where the shear stresses can be evaluated in a more more lifelike framework, making a comparison between the 2D and 3D representation of the pump possible. The method presented has the potential to enable the development of improved roller pump systems that cause less mechanical damage to cells.