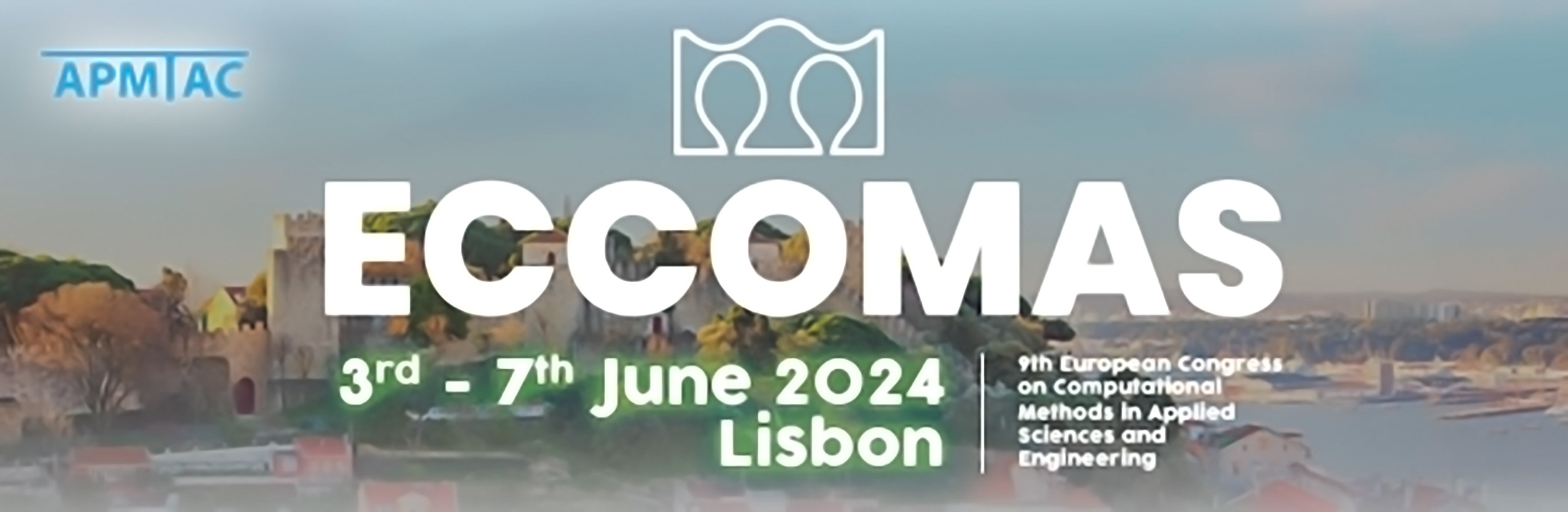
Fast simulation of overlapping beads geometry during wire laser additive manufacturing
Please login to view abstract download link
The objective is to propose a fast FEM strategy for simulating beads geometry during wire laser additive manufacturing for optimizing design and process parameters. The approach is based on the algorithm firstly proposed by Feulvarch et al. [1] for coatings. It is here notably improved and extended to 3D geometries by including the effect of the molten pool hydrodynamics resulting from buoyancy forces and the Marangoni’s effect. The simulation is very fast because it is carried out on a 2D mesh composed of linear elements that corresponds to the sole free surface of the liquid phase at each time step. Moreover, the implicit nonlinear resolution algorithm developed has the advantage of using diagonal matrices only. An example is proposed to clearly evidence the efficiency and robustness of the method developed in terms of geometry and CPU time.