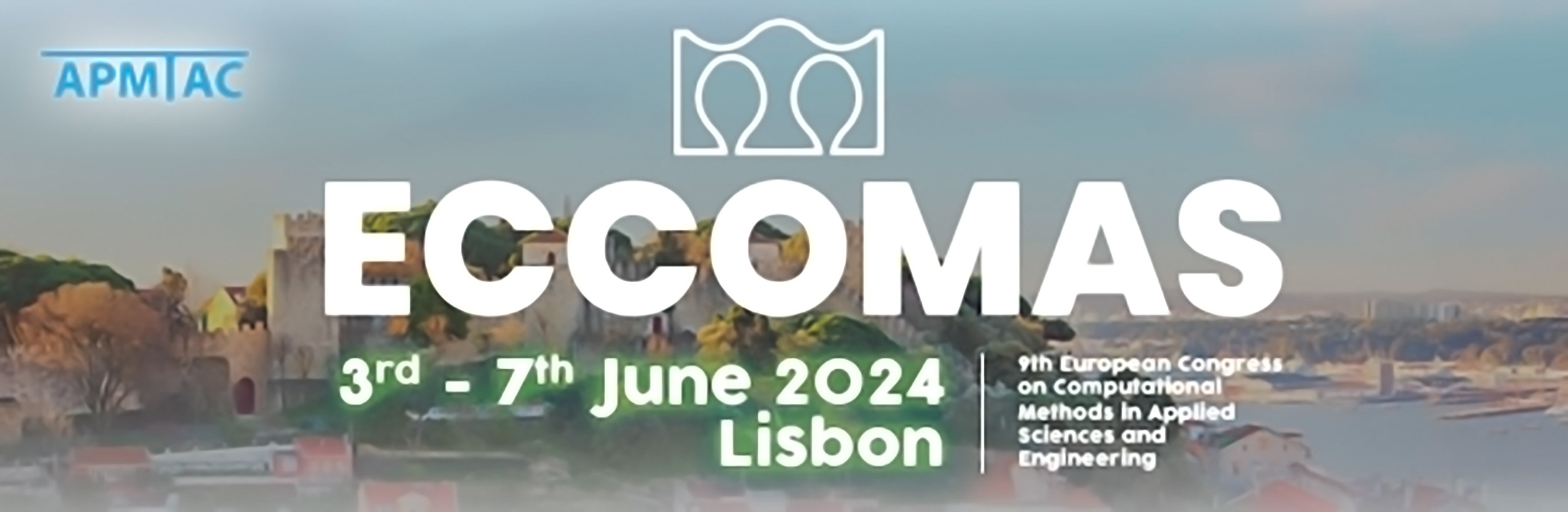
Using Bayesian Optimization for Cavity Shape Optimization in Injection Molding to Compensate for Shrinkage and Warpage
Please login to view abstract download link
In injection molding, shrinkage and warpage lead to shape deviations of the produced parts with respect to the cavity. Caused by shrinkage and warpage, these deviations occur due to uneven cooling and internal stresses inside the part. One method to mitigate this effect is to adapt the cavity shape to the expected deformation. This deformation can be determined using appropriate simulation models, which then also serve as a basis for determining the optimal cavity shape. We formulate an optimization problem to find the optimal cavity shape. The objective function measures the difference between the desired geometry and the warped geometry. This difference is computed by taking the average Euclidean distance of sample points on the surface of the deformed product on the one hand and the desired shape on the other hand. For the shape adaption we use free-form-deformation, which is a spline-based method, where the geometry is deformed based on the position of spline control points. Thus, the optimization parameters are the coordinates of the spline points which represent our geometry. Shape optimization usually requires a sequence of forward simulations, which can be computationally expensive. To reduce this computational cost, we use Bayesian optimization which uses Gaussian process regression as a reduced order model. Additionally, Gaussian process regression has the benefit that it allows to account for uncertainty in the model parameters and thus provides a means to investigate their influence on the optimization result. We present a Gaussian process regression trained with samples from a finite-element solid-body model. It predicts the deformation of the product after solidification and, together with Bayesian optimization, allows for efficient cavity optimization. Additionally, we undertake a comparative evaluation of various methodologies for determining the optimal cavity shape, focusing on computational efficiency and effectiveness of the method. The material parameters can underlie fluctuations due to different batches or when using recycled material. These uncertainties in the material parameters should be accounted for, such that the optimal shape results in low shrinkage and warpage as well as low variance with respect to the input parameters.