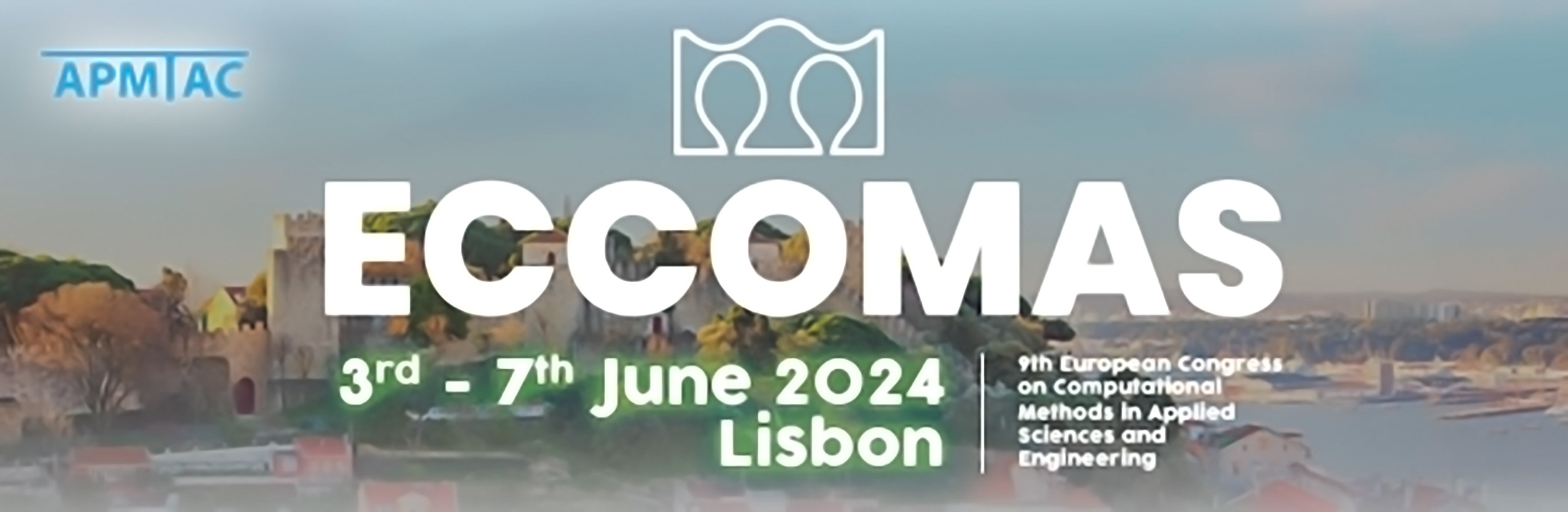
The Discontinuous Strain Method: Accurately Representing Fatigue and Failure
Please login to view abstract download link
Accurate modeling of unloading and reloading is crucial for fatigue simulation. Yet, traditional ductile damage models consider deformations after complete failure as irrecoverable, causing unphysical behavior during unloading. This unphysical behavior arises due to the continued accumulation of irrecoverable plastic strains after failure, where the post-failure strains are not recovered during unloading. Thus, erroneous stresses would arise at the point of crack closure. As a remedy, we introduce a discontinuity strain in the additive elasto-plastic strain decomposition, which absorbs the excess strain after failure and thereby leads to a more realistic unloading and reloading behavior. The proposed extension requires only minor modifications of conventional plastic-damage routines and only leads to a minor increase in computational effort. Furthermore, a characteristic length scale --- based on the discretization's resolution --- is employed to provide mesh-independent results. This new methodology is referred to as the discontinuous strain method. The theoretical aspects and algorithmic adjustments are first discussed for the one- and subsequently for the two-/three-dimensional case. For the sake of simplicity, the proposed method is presented with a basic ductile constitutive model and validated against established benchmarks from literature. However, the discontinuous strain method is independent of the constitutive model. Thus, elastic, plastic, and damage models may be chosen arbitrarily, thereby making the methodology applicable to low-cycle fatigue modeling. Additionally, the method can potentially be applied in other scenarios requiring a discontinuity representation within a plastic-damage framework.