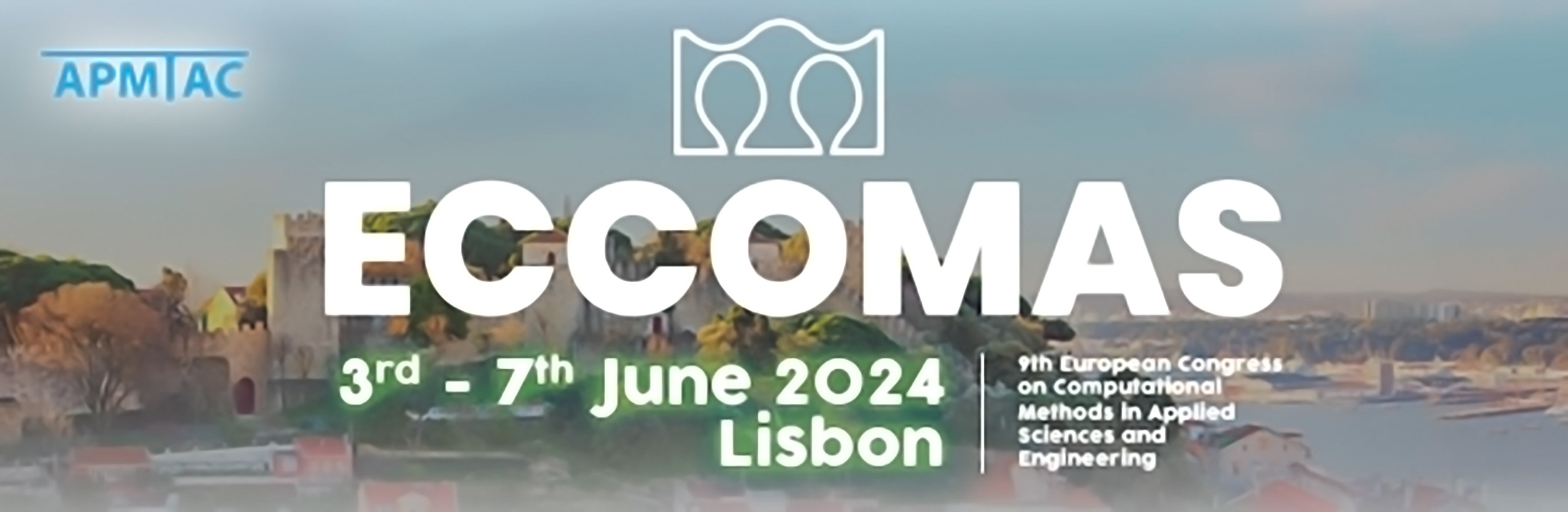
Modelling Melt Pool Dynamics Using The Particle Finite Element Method For The Simulation Of The Friction Melt Bonding Process
Please login to view abstract download link
High performance engineering designs often entail multiple materials. This introduces manufacturing challenges, especially in designs composed of dissimilar metals and when welding is the only joining mechanism tolerated by mechanical or design conditions. In this context, a promising process for welding aluminium and steel plates in lap-joint configuration is the Friction Melt Bonding (FMB) process. In the FMB, a cylindrical non-consumable rotating tool is pressed against a steel plate, generating heat by friction. Under the steel plate is the aluminium plate, and under this a thicker plate that serves as mechanical support and heat sink. The generated heat is transmitted to the aluminium plate by conduction, and if accurately controlled, will partially melt the aluminium plate forming a melt pool of liquid metal. The melt pool in the FMB process is visually inaccessible as it is trapped between the two dissimilar plates. In this context, numerical simulation is essential to support qualitative research on the FMB process or to predict behaviour in different fields of application. To simulate the process, this work proposes a partitioned methodology that combines PFEM (Particle Finite Element Method) and FEM. PFEM is used for modelling the aluminium plate, including phase change and convective flow within the melt pool. FEM, on the other hand, is used for the steel plate and the accompanying equipment, as they do not present complex multiphysics phenomena such as phase change. Simulation results were compared against experimental data and a good correlation was observed between the two approaches, at least for temperatures registered by thermocouples and the melt pool thickness.