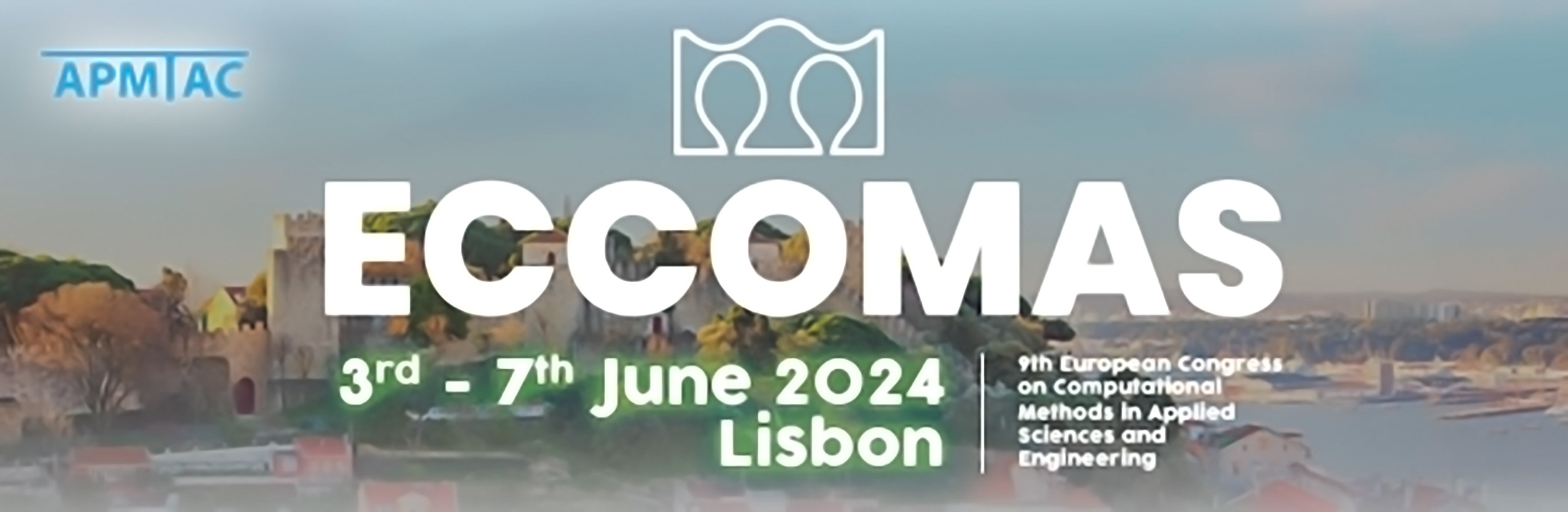
Advanced Numerical Methodologies For Thermo-Mechanical Simulation Of Metal Deposition Process
Please login to view abstract download link
Our current research aims at developing new approaches for the numerical simulation of Laser metal deposition (LMD) and Wire arc additive manufacturing (WAAM) which are two typical additive manufacturing technologies used for part repair and addition of new features on existing part. In both cases, the main and common issue is located at the interface between exiting part and the material deposit. This study is focused on the prediction of distortions and residual stresses at the scale of the bead deposit. Our thermo-mechanical modelling is based on mesh element activation algorithm for the material deposition. In a classical approach, a moving point heat source is applied on the new elements. The main limitation of this approach is the volume of new elements limited by the point heat source shape and therefore the time step must be sufficiently small to avoid discontinuous deposition. In our approach, the computational efficiency is improved by using line heat source with a large time step to replace the moving point heat source. For the sake of accuracy, the bead deposit topology is taking into account in the computational mesh. In our case study, the mesh includes interfaces between layer of bead deposit due to the use of different trajectory for each layer. Instead of using contact conditions, dynamic cohesive condition are applied at interfaces, linear combination are imposed on degrees of freedom which allows a size reduction of system linear to solve. We are currently in the phase of calibration and validation of our approach thanks to results of several experiments. We should obtain first numerical results in terms of distortions and residual stresses to be compared with experimental observations.