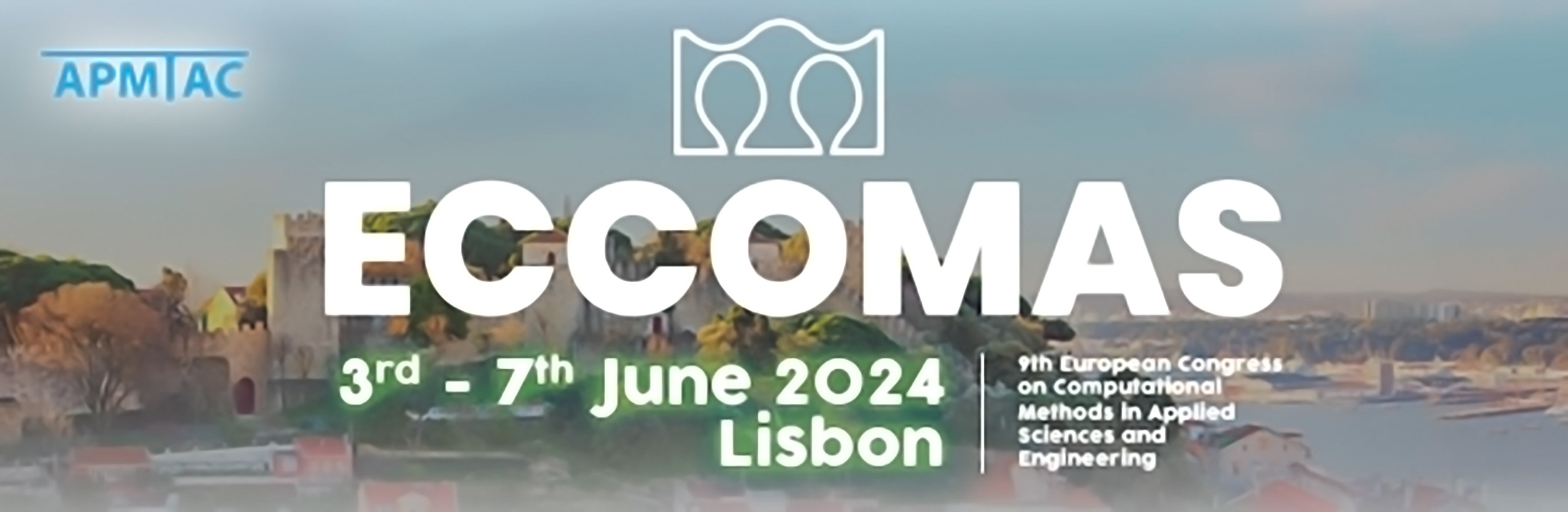
A Novel FEM Approach for the Analysis of Type-IV Hydrogen Storage Tanks Based on the Enhanced Refined Zigzag Theory
Please login to view abstract download link
Hydrogen is one of the best energy carriers for renewable energy storage due to its high energy density per unit mass. Type-IV composite pressure vessels are the current cutting-edge solution for compressed hydrogen gas storage and they represent the current state-of-the art for hydrogen fuel-cell vehicles. These multilayered composite vessels are generally produced by filament winding, a technology that allows for good flexibility in design and a very dense deposition of reinforcing fibre relative to the amount of matrix. Critical issues arise in the modelling by finite elements of the dome-shaped tank structure, since in this area both the thickness and the fibre orientation of each layer vary as a function of the radius and the laminate can be globally thick. These properties cause finite-element modelling using 2D First-order Shear Deformation Theory (FSDT) to be inaccurate, on the other hand, a much more accurate discretization with solid 3D elements leads to computationally costly models. The present paper investigates the modelling of multilayered composite pressure vessels by means of shell finite elements based on the enhanced Refined Zigzag Theory (en-RZT). en-RTZ, originated from the FSDT, is adopted to provide accurate and computationally affordable predictions of the global responses for thick laminates with high transverse flexibility and heterogeneity. The study highlights the accuracy and robustness of the developed elements with respect to the complexity of the vessel’s stacking sequences. The accuracy and computational burden of the proposed approach is assessed by a comparison with shell finite elements present in the commercially available software.