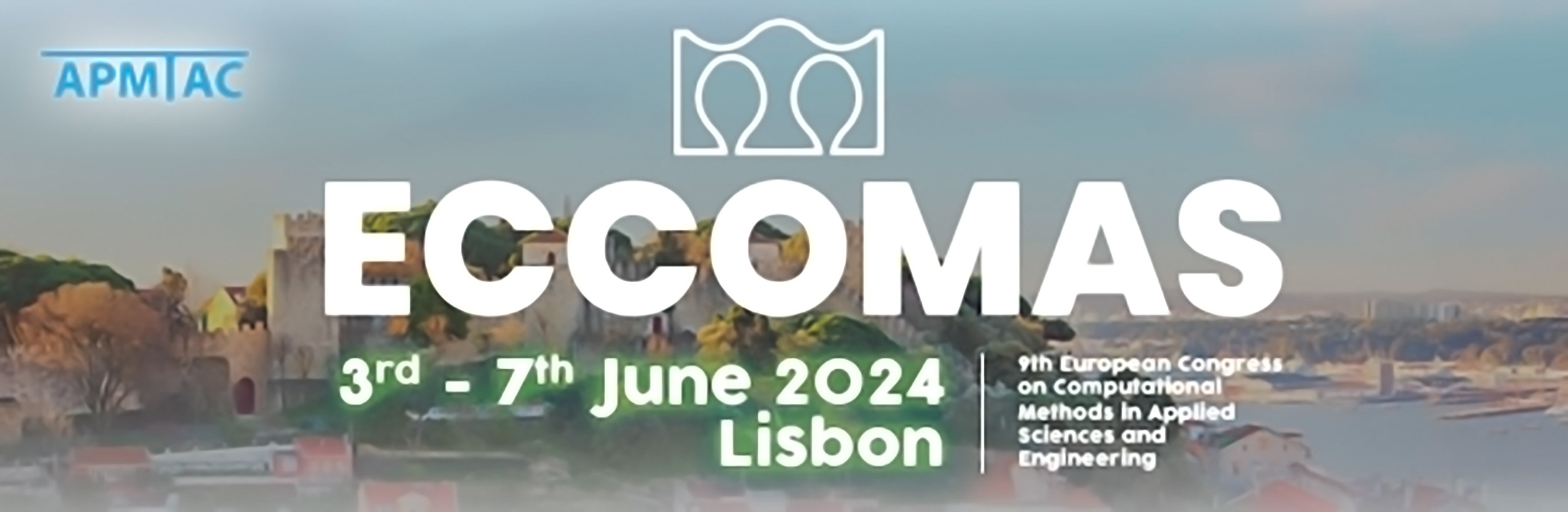
Multidisciplinary optimization of a heat exchanger using lattice structures accounting for additive manufacturing constraints
Please login to view abstract download link
In the scope of the RECET4Rail European Union (EU) project we aim at better understanding how Additive Manufacturing (AM) technologies can contribute to Traction Drive (TD) sub-systems through the development and manufacturing of new type of heat exchangers based on lattice structures. In particular, we focus on the design of an AM-based heat exchanger through a Multidisciplinary Design Optimization (MDO) process. We show how the GEMSEO framework can be used with several features to implement the optimization process from industrial tools despite the complexity of the problem and accounting for several practical constraints. The process is based on three chained tools which are wrapped into GEMSEO disciplines: (1) a CAD builder (2) an automatic mesher based on ANSYS DesignModeler and Meshing, (3) a coupled fluid-thermal model, implemented through the ANSYS Fluent solver. Platform services from GEMSEO are used to handle the distributed executions of the process thanks to ssh-based disciplines and sheduler-based disciplines. The optimization problem is formulated in order to minimize the thermal resistance of the heat exchanger subject to an allowable pressure loss. The design variables characterize the shape of the lattice structures such as radii, orientations, cell density which potentially lead to a huge dimension. Manufacturing constraints have been taken into account through the range of design variables in order to ensure minimal diameters, limited overhanging and free path for powder removal. In addition, the outputs of the chain are not differentiated with respect to the inputs which prevent the use of gradient-based algorithm. This complexity is limited by reducing the number of design variables through control points values interpolation, and separating the global analysis into three phases: (1) an initial Design Of Experiment (DOE) with a sensitivity analysis, (2) an optimization based on surrogate models built from the initial DOE, (3) a direct gradient-free optimization. Through this analysis, we show how GEMSEO can be conveniently manipulated to converge toward an optimal solution that satisfy the constraints and enabled to gain 28% on the thermal resistance with a pressure loss increase of 42%, while satisfying the allowable pressure loss.