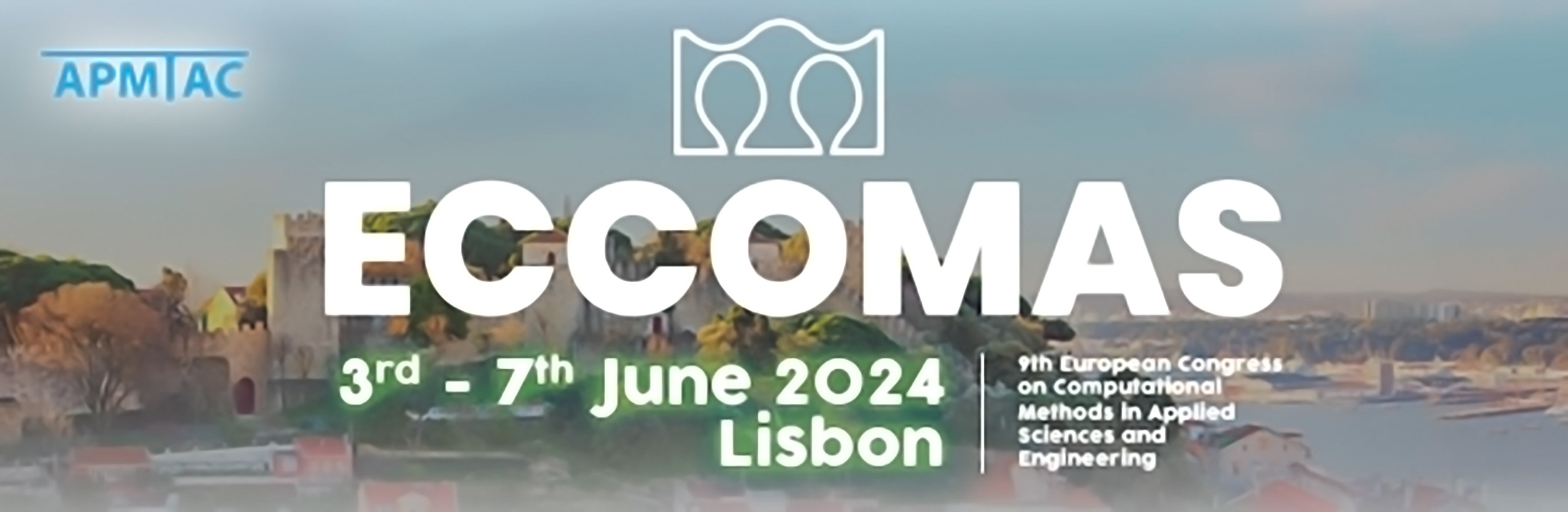
Reduced Order Model for Temperature Field Simulation of Wire Arc Additive Manufacturing
Please login to view abstract download link
Additive manufacturing (AM) has revolutionized the manufacturing industry, offering a new paradigm to produce complex geometries and parts with customized properties. Among the different AM techniques, the wire arc additive manufacturing (WAAM) process has gained significant attention due to its high deposition rate and low equipment cost. However, the process is characterized by a complex thermal history making it challenging to simulate it in real-time for online process control and optimization. In this context, a reduced order model (ROM) using the proper generalized decomposition (PGD) method [1] is proposed as a powerful tool to overcome the limitations of conventional numerical methods and enable the real-time simulation of the temperature field of WAAM processes. These simulations use a moving heat source leading to a hardly separable parametric problem, which is handled by applying a novel mapping approach [2]. This procedure makes it possible to create a separated representation of the model, which is required to apply the PGD method, allowing a simulation of multiple layers. In this contribution, a PGD model is derived for the temperature field simulation of the WAAM process. A layer-by-layer simulation in combination with a compression of the PGD modes, without influencing the approximation error, is shown. The compression is an essential step since the modes sum up quickly over the layers and thus a reduction of the number of modes is needed. Furthermore, using an element birth technique leads usually to an update of the mesh or a new mesh in each time step. Though, this is not the case applying the mapping approach, where only a single nonchanging mesh is required to simulate the deposition of a whole layer.