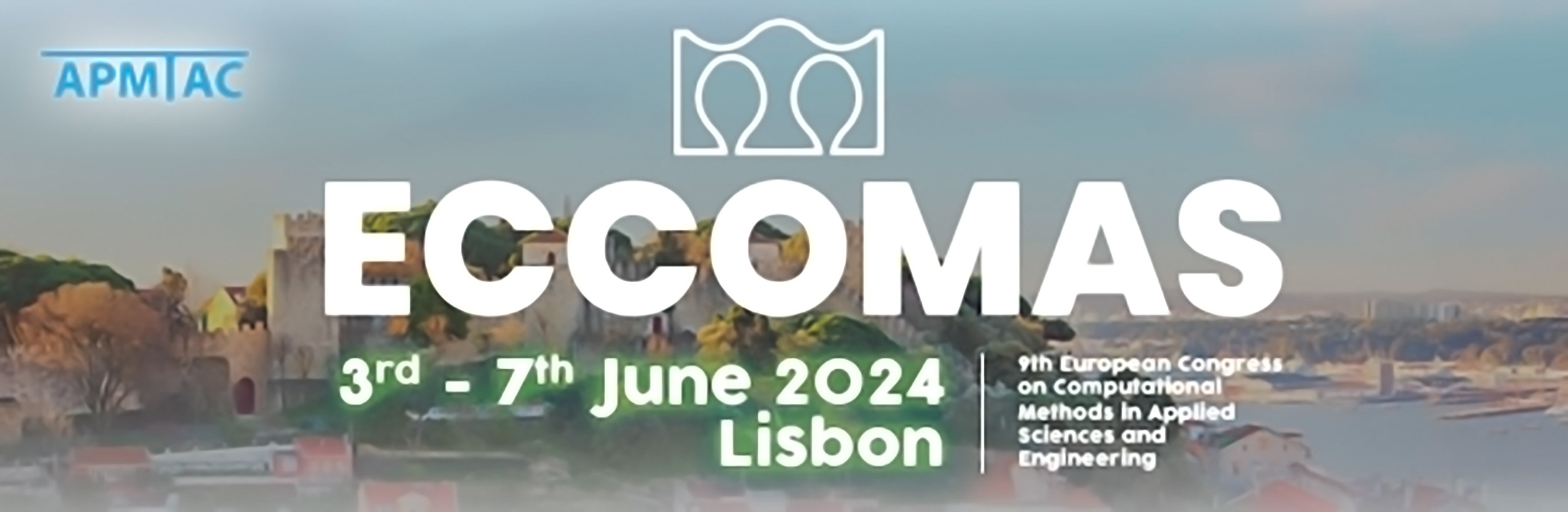
Generating support structures for Additive Manufacturing using topology optimization and AM-guidelines
Please login to view abstract download link
Additive Manufacturing (AM) has caught interest in a variety of industrial sectors, which has promoted the advancement of this technology at accelerated rates. Nowadays, it is even possible to produce functional components at home using desktop 3D printers. Many of these printers are used to manufacture amusement designs, mechanical spare parts, or prototype parts, many of which have a defined and unalterable geometry. Most of these designs have overhanging parts that demand the unavoidable use of support structures and therefore raise production costs and plastic waste, the latter being a major environmental concern. This work focuses on the design of support structures for desktop 3D printers. The idea is to generate supporting structures that are easy to remove, that consume a low amount of material but that guarantee the mechanical support of the part during 3D printing. The proposed methodology uses the topology optimization technique with size control. Specifically, we use the density method under the robust formulation to control the minimum size of solid members and cavities. In addition, maximum size and minimum gap restrictions are used to increase the geometric control in the support design. The topology optimization problem is fed back with a set of geometric guidelines collected for a particular desktop 3D printer that operates on PLA. Specifically, we use reference designs to evaluate the critical distance between supporting columns, the maximum aspect ratio, the critical overhang angle, and the minimum size of supporting columns and cavities. The geometric guidelines are strategically included in the topology optimization problem equipped with size control, in order to produce efficient supporting structures for Additive Manufacturing. The study is carried out in two-dimensional designs that are extruded to generate the bulky part in an experimental verification step.