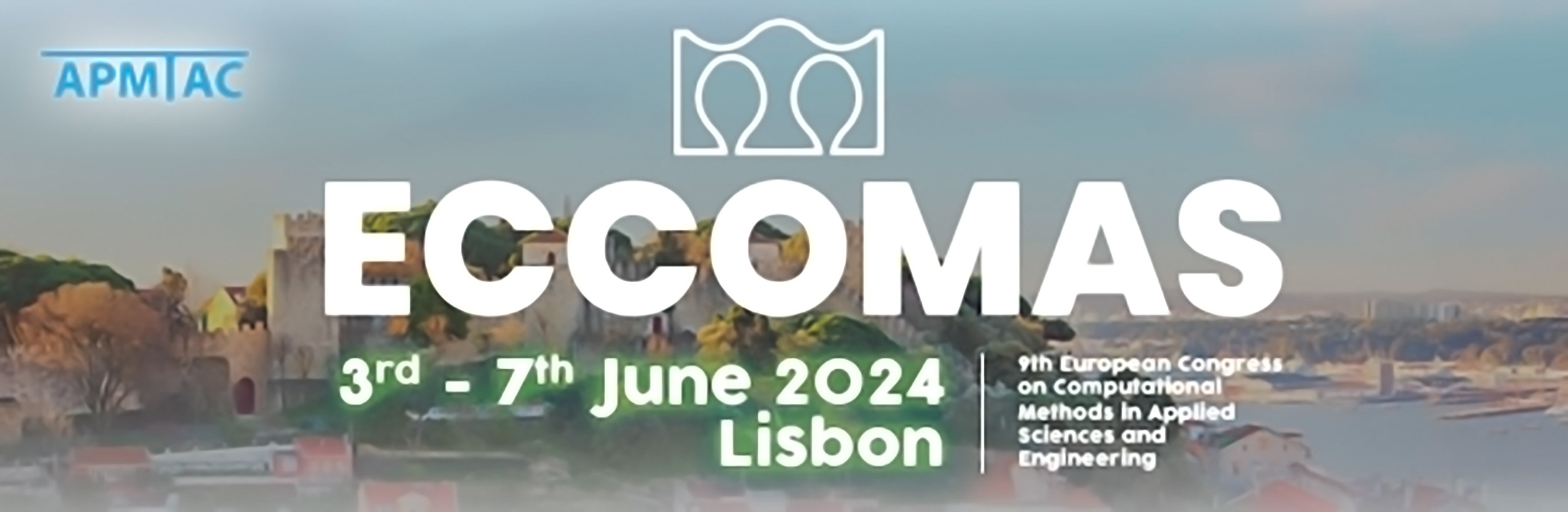
3d Reconstruction and Finite Element Modeling of Additively Manufactured Lattice Architectures
Please login to view abstract download link
The study of cellular materials, especially triply periodic minimal surfaces (TPMS) and their properties has gained considerable significance due to the advancement in additive manufacturing technologies. TPMS architectures are found to have high stiffness-to-weight ratio, high strength-to-weight ratio and energy absorption capacity. Finite element (FE) techniques have been widely used to study the deformation mechanisms and failure modes of these complex architectures [1]. However, due to the defects generated during manufacturing, finite element modeling of an ideal geometry does not perfectly predict the lattice's mechanical performance. In the present study, a detailed finite element analysis is performed by reconstructing the 3D printed lattice architecture and including the manufacturing defects into the model. Micro-computed tomography (μCT) images of the 3D printed samples were generated to quantify the internal defects generated during manufacturing. 3D reconstruction of the test sample was done using these μCT scans to characterize the size and the spatial distribution of pores within the sample. Finite element models were then generated using the reconstructed geometry and the porosity distribution was then mapped to the FE model to accurately predict the mechanical performance of the lattice architecture. Surface deviation from the ideal geometry was measured by comparing the differences from the reconstructed geometry to the ideal geometry. Mechanical properties of the build material were extracted from tensile tests performed on the samples in 3 different directions to incorporate material anisotropy in the material model. Appropriate damage models were selected to accurately predict the deformation and failure mechanisms under compression loading. Finite element simulations were carried out in ABAQUS and the results were compared against the experimental response as well as with the results obtained using ideal lattice geometry. By incorporating the manufacturing defects into the reconstructed geometry, the finite element model was able to predict the mechanical response and failure similar to the experimental findings. This method eliminates the assumptions while using an ideal geometry and gives insight into the various failure modes under lattice compression which will be helpful in the selection of optimal lattice designs for various mechanical applications.