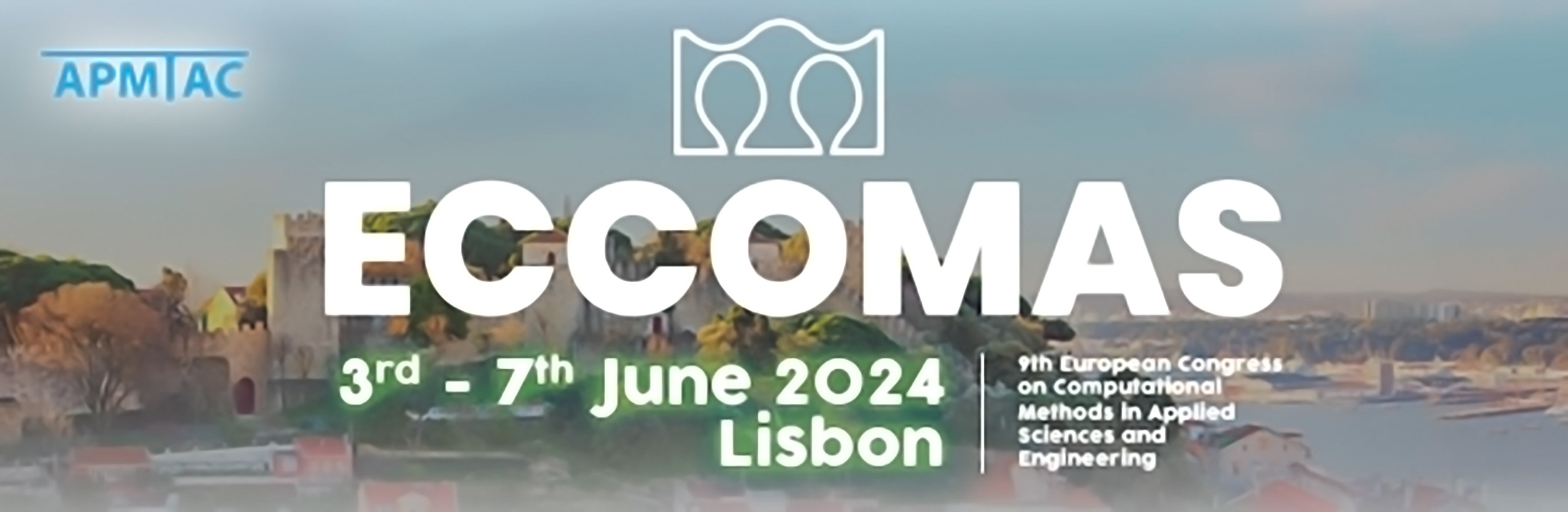
Coupling grain growth and anisotropic mechanical behavior at track scale by thermal-metallurgical-mechanical simulations
Please login to view abstract download link
During the laser powder bed fusion (L-PBF) process in metal additive manufacturing, the formation of columnar dendrites-based microstructures along the construction direction is observed due to high-temperature gradients. This resulting anisotropic microstructure causes variances in mechanical properties between construction and scan directions, leading to potential distortions or damage in thin-walled structures. Our objective is to concurrently characterize grain structure and anisotropic mechanical behavior during L-PBF, focusing on investigating hot cracking formation through thermal-metallurgical-mechanical simulations. Grain morphology will be analyzed using an established model integrating grain growth simulation with thermal and fluid mechanics modeling. The Cellular Automaton (CA) method is employed to simulate grain growth and nucleation within the mushy zone. A unified framework utilizing 3D finite element/level-set (FE/LS) formulations tracks melting pool morphology via established thermal and hydrodynamic models. Additionally, anisotropic elasto-viscoplastic behavior will be studied using the Crystal Plasticity (CP) model, considering slip systems of individual grains to understand stress distribution based on crystallographic outcomes. Our thermal-metallurgical-mechanical simulations aim to examine mechanisms generating microscopic residual stresses and defects, notably focusing on structural effects. This includes studying deformations at grain boundaries, intra-granular textures, inherent intergranular residual stress formed during solidification, and their potential influence on material mechanical responses. Insights gained from these analyses will contribute to the development of a new criterion for predicting hot cracking.