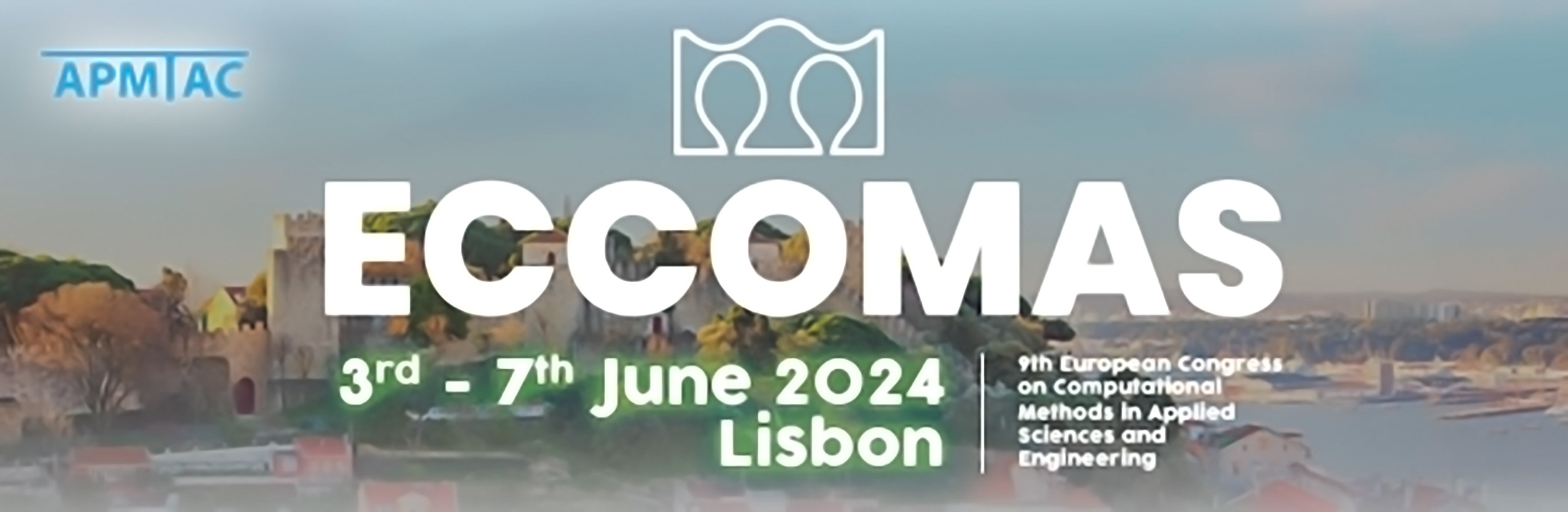
Accelerated Additive Manufacturing Simulation Through Inherent Strains Meta-Models Trained With Generic Databases
Please login to view abstract download link
Nowadays, additive manufacturing through direct energy deposition is a major technique for producing metallic pieces for increasingly demanding structural applications. Current trends demand the characterization, and eventual limitation, of the differences between “as-designed” and “as-manufactured” when printing as a necessary step towards the final goal of producing in a First-Time-Right fashion. Numerical simulation has proved to be a very useful tool in achieving these objectives. The main goal of the presented research is to develop and implement a numerical methodology able to trustworthy predict the distortions of printed parts with complex geometries in a fraction of the time required by standard techniques. Generally speaking, this methodology consists of two main building blocks. The first off-line block uses a thermo-mechanical transient model on simple geometries to get the inherent strains for each of them. Then a meta-model relating basic geometric features with the inherent strains is built. The second on-line block consists of an elastic FEM computation in which each macro-layer is segmented into simple polygons whose geometric features are used to get the corresponding inherent strains to be injected in the FEM computation. The main intention of this communication is to present the results and main conclusions of the development and testing of this methodology which has been found effective when predicting distortions compared with full thermo-mechanic simulations, reducing the computational time of the on-line stage from days to a few minutes.