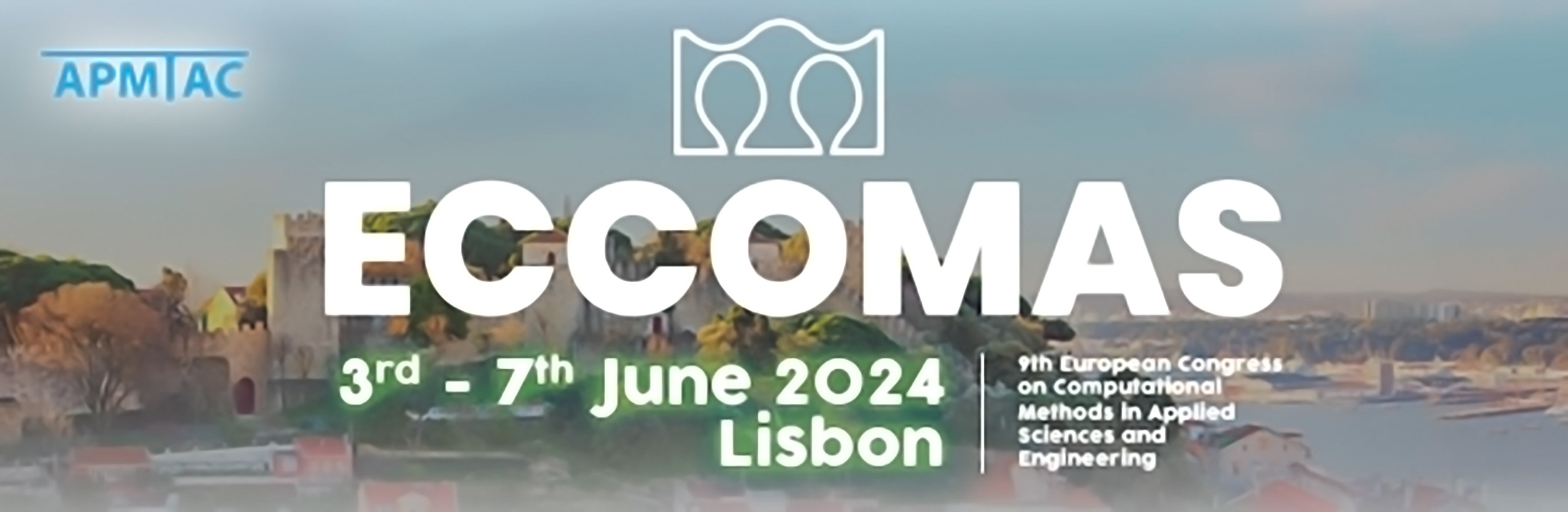
Computational Geometry Generation of Concept Design Driven by WAAM Manufacturability
Please login to view abstract download link
Inspired by the highly advanced manufacturing process of Wire Arc Additive Manufacturing (WAAM), yet poorly explored in linking fabrication constraints and Computational Design (CD), the main objective of this research is the automatization of process-tailored concept design development. In the current industrial design workflow three main phases can be highlighted: formation, which leads to a concept design; evolution, which leads to an advanced design through digital tools such as Computer Aided Design (CAD) and Computer Aided Engineering (CAE) for computational multidisciplinary optimizations; manufacturing, which changes the optimized design afterwards, or influences the initial one, having digital fabrication processes (CAM) as the main source of digitalization. In contrast to the last two phases, the formation does not fully exploit computational algorithms, and concept designs are currently defined manually. Since manufacturing feasibility is rarely systematically addressed at this stage, the evolution phase could lead to optimized non producible designs, and the useful case of manufacturable but non-optimized designs is not contemplated. Additionally, more sustainable production processes, along with material and resources minimization, are needed. Thanks to the calibrated deposition, by adding material only where needed, WAAM may answer to this necessity, in combination with CD. To address these challenges, a novel CD approach, inspired by form finding of minimum surfaces as discussed in Updated Reference Strategy [1], is proposed. The goal is to simultaneously generate process-specific and thin-wall industrial concept geometries of functional components together with production data from scratch. Starting from given geometric boundaries to be connected and a set of control variables, WAAM manufacturability constraints (e.g., layer height) will be considered as main driver parameters of the shaping. In the attempt of establishing a connection between the common advanced industrial design tools (CAD, CAE) and the industrial manufacturing (CAM) information, to solidly link the geometry generation and the manufacturability assessment, the node-based shape optimization will be therefore integrated with a geometric interpretation of the constraints coming from manufacturable printing paths [2]. To validate this approach, the method developed is applied to a simplified geometry derived from the use case of an A-pillar node of a car body structure.