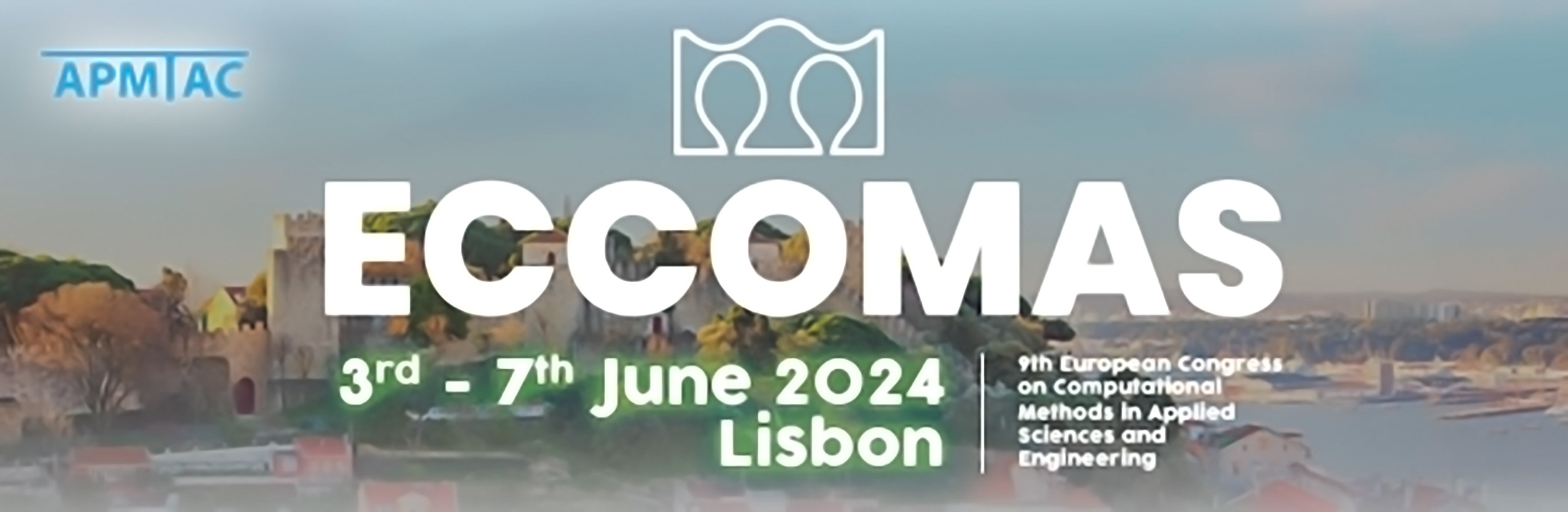
Weight Optimization Using Design Topology And Multi-Materials for AM Application in MULTHEM Project
Please login to view abstract download link
Mechanical products such as EV Batteries and Electrical Motors have housings confined to their boundary spaces. Existing industrial products use metal like aluminium as a full-covered casing or housing material, and this is costly in terms of performance overall as weight is a major affecting factor. With the use of metal-polymer 3D printing technologies, designs can be optimized for weight, and thus, the performance. In MULTHEM project, a new approach in Additive Manufacturing (AM) has been researched for designing such housings to reduce weight and to improve thermal management by using design optimization and new developed multi-materials composed of Reinforced Carbon Fiber Composites (RCFC) and aluminium combinations. This is virtually applied on housings of use-cases (an EV battery and an electric motor) in a modelling and simulation environment. The Finite Element Analysis (FEA) and Topology Optimization with multi-materials (metal-polymer) has been simulated on the housings. The heat dissipation in these components to the environment has also been taken into account in the design optimization where a balance is required between heat transfer and mass reduction through the material thickness. Limitations in design topology optimization process occur with less material thicknesses in the housings where no further reduction in mass is possible as constraints from 3D printing processes are applicable. Results show significant reductions in housings mass up to 50% compared to original metal designs. This further enhances the capabilities in Design for Additive Manufacturing (DfAM).