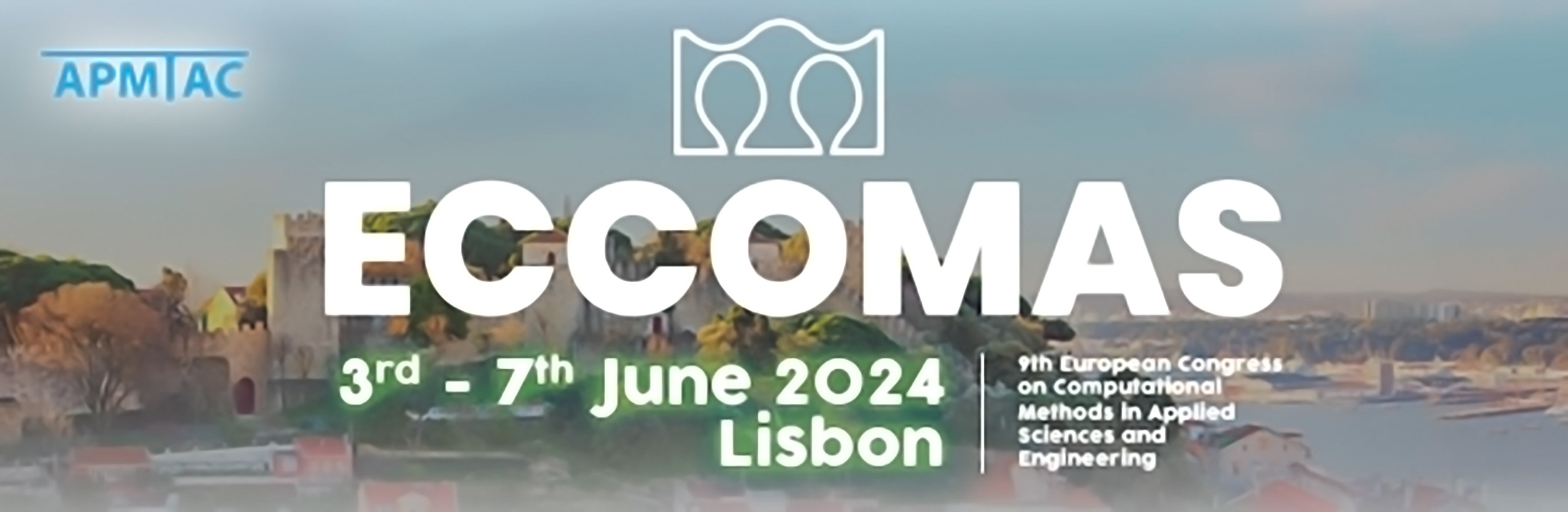
Verification, Validation and Uncertainty Quantification Applied to Composite Space Structures
Please login to view abstract download link
Aiming at reduction of time-to-market and cost, the development and qualification of space structures rely more and more on numerical simulations of the structural behaviour. The knowledge gained in the qualification of the metallic inter-stage 1/2 of the Vega-C launcher by simulation for stiffness behaviour [1] has been further developed to demonstrate the simulation capabilities for qualification of a composite engine thrust frame for stiffness and strength behaviours. A VVUQ framework [2] has been set-up for the validation of simulations predicting the stiffness and the strength of a composite engine thrust frame. To define the validation hierarchy, the design of the engine thrust frame was decomposed into subsystems, structural details and laminates (Figure 1). The subsystems and structural details were tested and corresponding simulation models have been established. Uncertainty quantification of the simulation quantities of interest was performed and the resulting cumulative distribution functions have been compared to those obtained from the test results using the area metric. At laminate level, plain strength and open hole tests and simulations have been performed. The laminate has been modelled at the meso scale and both intra- and inter-laminar damage initiation and progression have been considered. Based on sensitivity analysis, the simulation input parameters were ranked. Designs of experiments were set-up to construct surrogate models predicting the simulation quantities of interest for the selected input parameters. The acquired strategies from the validated simulations have been applied to the simulations of the structural details. The structural details consist of bolted joints and equipment brackets, which were also tested in order to validate the corresponding simulations. In addition, the bolted joint tests and simulations have been used to calibrate idealized fastener models that are used at the higher levels of the hierarchy, i.e. subsystem and system (engine thrust frame) level simulations. The proposed VVUQ framework allowed to provide an adequate blind prediction for the test of the full-scale structure that was performed to prove the methodology for building credible simulations. The framework paves the way to eventually eliminate expensive full-scale testing from the qualification process.