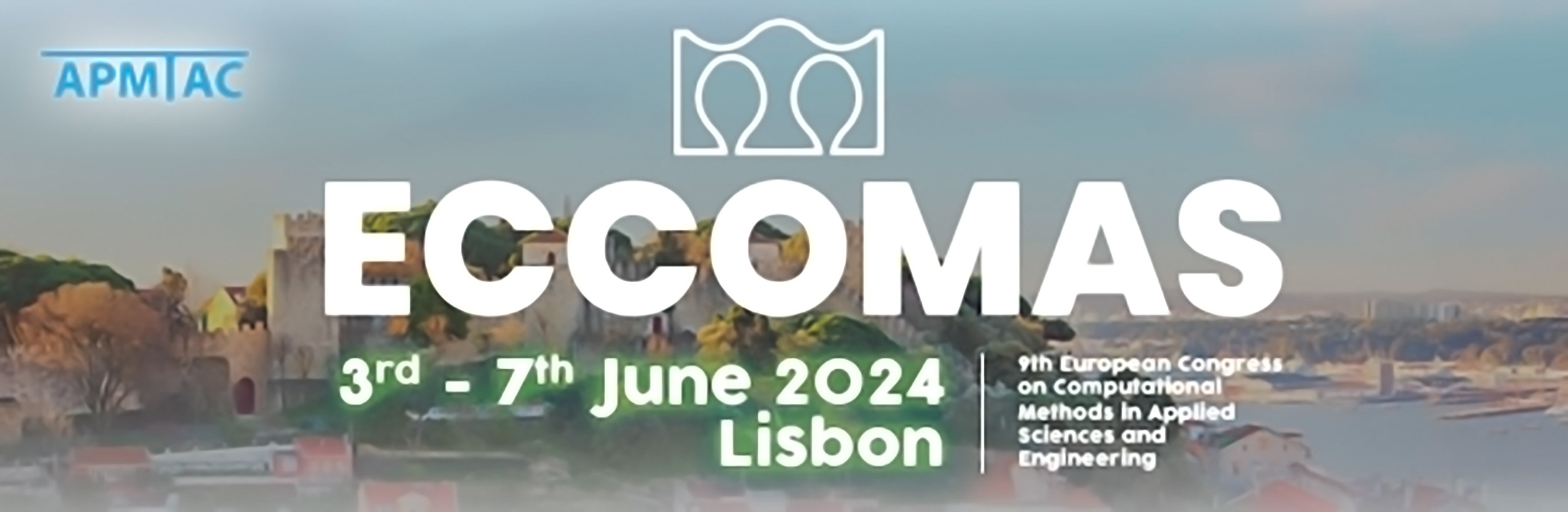
Semi-mechanistic Prediction of Residence Time and Mixing Dynamics using a Machine Learning-based Convection-Diffusion Model
Please login to view abstract download link
The dynamics of mixing is an important metric to consider in many industrial processes, such as extruders, blenders, mixers/granulators and reactors. This is because it directly influences the quality of the product, specifically the homogeneity of materials. In extrusion processes, mixing can also influence product properties such as the viscosity and porosity of the product. A common measure of mixing dynamics is the residence time distributon (RTD), which represents the probability distribution of the time that material remains within a system. Typically, RTDs are determined using tracer pulse tests obtained via experimental or intensive computational approaches (i.e. CFD, DEM). However, due to the time consumption and computational intensity required with the aforementioned methods, there is a need for a computational efficient method to predict RTDs. This work addresses this need by using a hybrid equation based model, specifically a 2-dimension, compartmental convection-diffusion model, which is coupled with machine-learning (ML) algorithms. The ML component is used to predict variation in velocity fluxes thoughout the extruder and at different process parameters. These predicted fluxes are then used as inputs to the convection-diffusion model. Another mixing metric that commonly used is the relative standard deviation (RSD), which indicates blend uniformity. In addition to RTDs, RSDs can also be predicted from the compartmental convection-diffusion model, which further motivates the use of this model. The model framework developed in this study acts as a computationally-efficient reduced order model of a high-fidelity CFD model for predicting mixing dynamics, with the ability to provide RTD predictions in under 5 seconds as opposed to the 44 hours required for the CFD model, for one run. This model was calibrated and validated using data generated from CFD modeled starve-fed extruder, where process conditions (screw speed and throughput) were varied. The model validation indicated good predictive performance, with R-squared values of above 0.9 obtained. Due to the computation efficiency of this model framework, optimization tasks could also be carried out, to determined optimal process parameters for the desired mixing metrics.