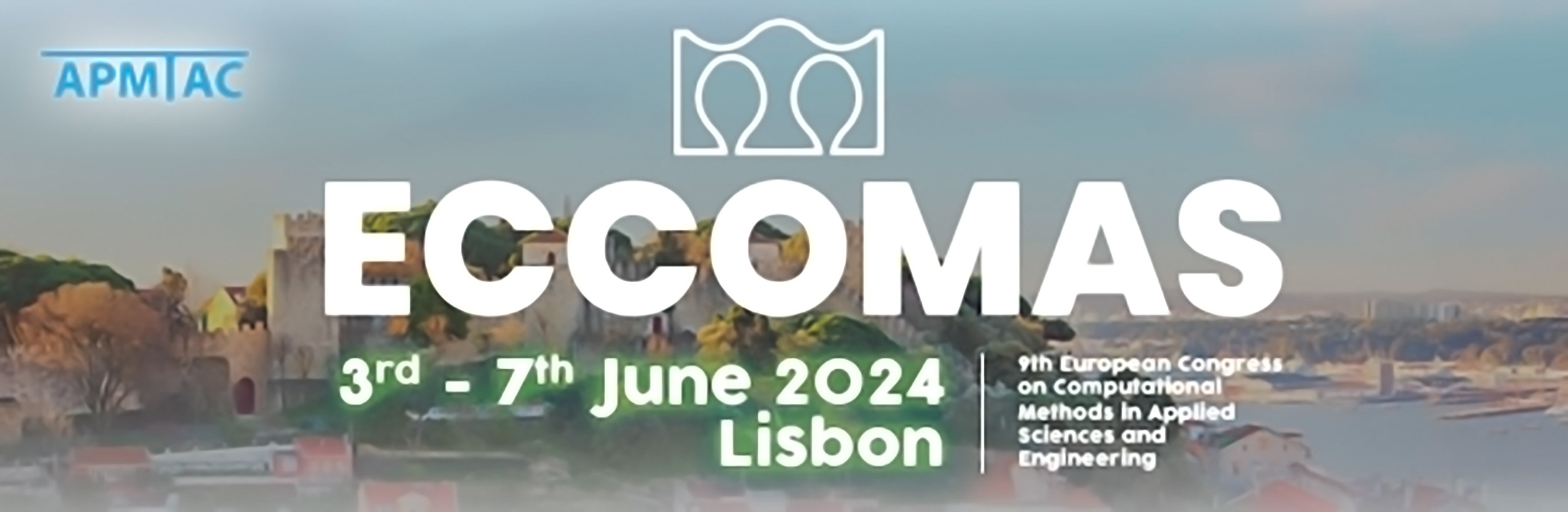
Modelling and Simulation of High Velocity Impact of Particles in Cold Spray Additive Manufacturing
Please login to view abstract download link
Cold spray additive manufacturing (CSAM) is an emerging technology with high deposition rate and high efficiency, that relies on the high-speed self-consolidation of powder particles to build up layers of material for diverse applications (e.g., coating, repairing and bulk component). In this paper, a comprehensive study is carried out on the modelling and simulation of high strain-rate deposition behaviour and interfacial bonding of highly deformed particles during the CSAM of aluminium powder. Both single particle and multi particles configurations are investigated using three-dimensional models with ABAQUS / Explicit solver. To capture the particle complex deformation mechanism, rate-dependent elastoplastic damage constitutive model is adopted. The initial temperature is set at room temperature, while the initial velocity is set at a critical value to ensure particle bonding. The developed model relies on coupled Eulerian - Lagrangian (CEL) approach. As a mean of solving high strain rate deformation problem, CEL combines the advantages of both frameworks to capture the complex particle-particle interactions with good computational accuracy. The evolution of particle shape, residual stress, equivalent plastic strain and temperature during the collision for both single and multi-particle models are presented. Through the particle impacting simulation, it is found that the strain localization mainly occurs at the interfacial region due to the thermal softening. The phenomenon of adiabatic shear instability and the resulting heat dissipation, which occur at the interface, are the main driving force behind the bonding between the particles and the substrate on the one hand, and between the particles on the other. They promote jetting splashing with inhomogeneous deformation. Through the multiple particles impacting simulation, it is possible to predict the compressive residual stress after collision induced by shot peening and bonding effects. It is also possible to predict the surface topology as well as the porosity. In summary, this research advances the understanding of particle deposition behaviour in CSAM through the development of multi-physics particle impacting models. The insights gained from two proposed models can contribute to the optimization of CSAM parameters, enhancing the precision and efficiency of the deposition process across a range of industrial applications.