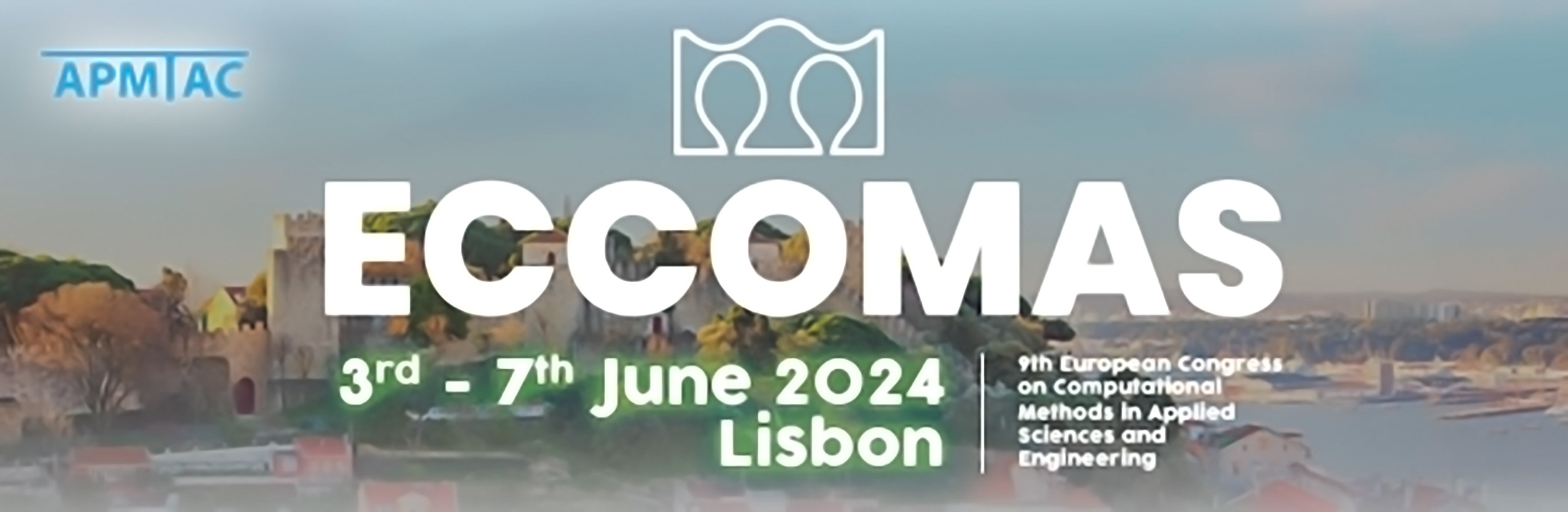
Implementation of micro-mechanical models for micro-structural based characterization of Cohesive Zone Modeling (CZM) parameters for diffusion bonded components
Please login to view abstract download link
Multilayered aluminum components are of great interest in the aerospace industry due to their high strength-to-weight ratio and corrosion resistance. One of the common production methods of such component is diffusion bonding. For load bearing applications the bond strength between the different layers is critical. Alongside experimental techniques for assessing bond strength in layered components, a computationally efficient method to model interface failure is the cohesive zone (CZM). In this framework the mechanical response of the interface is governed by a traction-separation law (TSL). The TSL represents the relation between the stresses across the interface and the relative displacement between layers, capturing the loss of load-bearing capacity before the final separation. The TSL parameters are commonly determined by fitting of experimental load displacement data and numerical simulations. In such an approach, micromechanical aspects such as bonding defects due to oxide layer fracture along the interface, which are known to greatly influence the bond strength, cannot be directly taken into consideration. The goal of the current study is to utilize a micromechanical based FE approach in conjunction with a Continuum Damage Model (CDM) approach to determine the TSL parameters, of diffusively bonded aluminum 7075 specimens, solely based on the defects pattern observed at the interface and a ductile failure law for Al 7075. First the flow-stress of Al7075 at temperatures of 400-500C was determined by cylindrical compression experiments and finite element modelling. Next, Al7075-Al7075 specimen pairs underwent diffusion bonding at 400-500C and thermo-mechanical finite element modelling was used to compute the time dependent thermo-mechanical fields at the specimen interface. Following the bonding experiments, small tensile specimens were cut from the bonded pairs and underwent characterization of the interface using a Scanning Electron Microscope (SEM) and subsequent mechanical testing. The interfacial morphology observed from the SEM imaging was used to construct microstructural based Representative Area Elements (RAE) of the interface area. To model intact bond failure of the Al7075 in the RAE, a continuum damage approach for Al7075 previously published by the authors was used. It is demonstrated that effective TSL can be obtained from the micromechanical models which explicitly take micro-structural parameters of the interface into consideration.