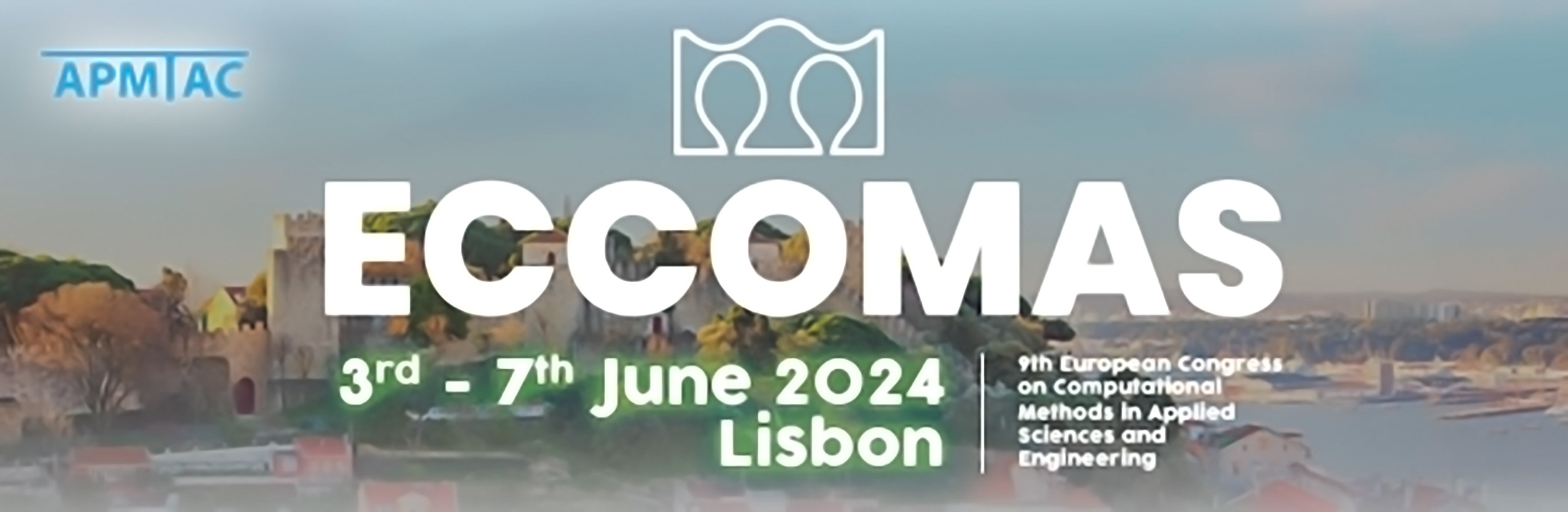
Ductile Fracture Analysis Using an Evolving TSL Along The Crack Path
Please login to view abstract download link
Ductile fracture is characterized by large inelastic deformation, formation of highly localized zones of intense straining such as necking and, ultimately crack propagation leading to failure. The material behavior in the failure process zone after crack propagation is affected by the interaction between the necking and cracking phenomena. In this contribution, XFEM is used with a traction separation law (TSL) to model the interaction between these two localization phenomena present in ductile metals. The novelty of this contribution is that the traction-separation law evolves during the analysis, and therefore, the TSL at a discontinuous surface may vary along the crack path. The transition and interaction between the two localization phenomena is governed by different segments of the TSL. Woelke et al. [2] also showed that the TSL evolves as a function of crack extension, where a pre-defined varying TSL along the crack path is used. However, in this contribution, the varying TSL comes automatically during the analysis as the law is affected by the stress state and necking evolution in the failure process zone and region ahead of the crack tip. In addition, this approach also relieves a user from having a pre-defined TSL. A solid-like shell element [1] is used in the finite element analysis of thin sheets which is superior to a shell element and a solid element in terms of modelling and computational efficiency, respectively. The proposed approach is validated by comparing the finite element analysis results with experimental results in middle-crack tension tests and shear tests of steel specimen. REFERENCES [1] A. Ahmed, F. P. Van der Meer, and L. J. Sluys. “A geometrically nonlinear discontinuous solid-like shell element (DSLS) for thin shell structures.” Computer Methods in Applied Mechanics and Engineering 201 (2012): 191-207. [2] P.B. Woelke, M.D. Shields, and J.W. Hutchinson. “Cohesive zone modeling and calibration for mode I tearing of large ductile plates.” Engineering Fracture Mechanics 147 (2015):293-305.