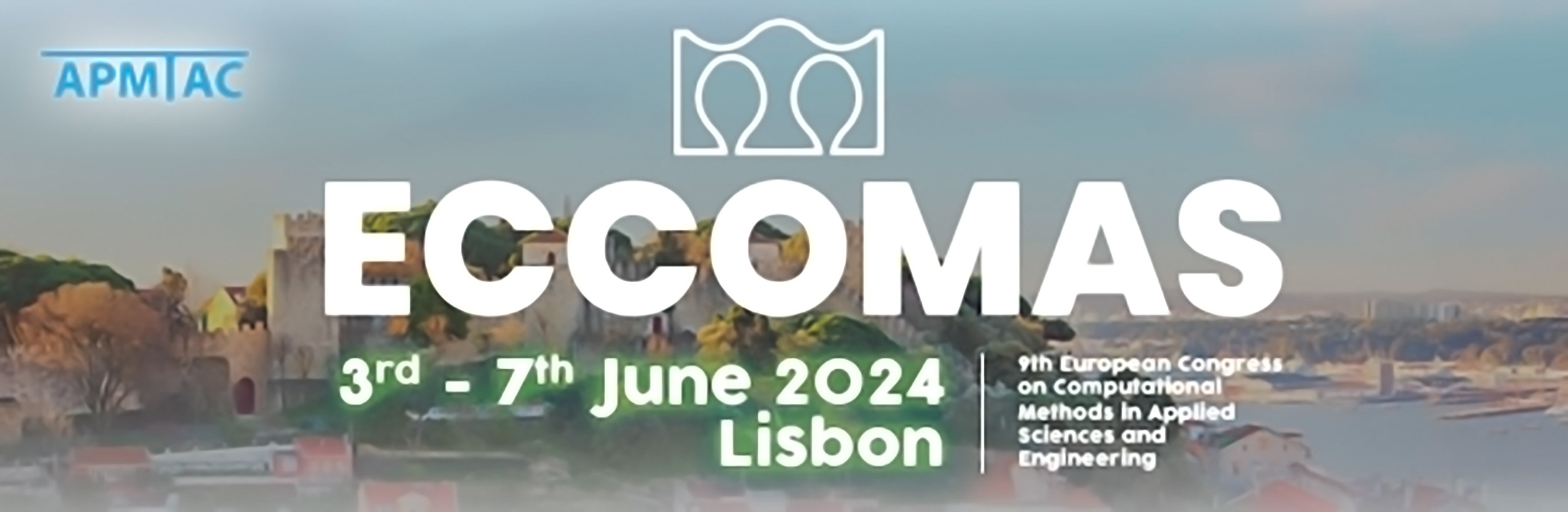
Modeling of 3D Printed Soft Pneumatic Actuators
Please login to view abstract download link
Soft Pneumatic Actuators (SPAs) are characterized by a rather simple structure with a series of inner chambers that are pressurized to trigger a deformation and produce forces. In this context, Additive Manufacturing (AM) was successfully applied to produce enhanced SPAs by exploiting design freedom and customizing them for specific tasks. A faithful prediction of the behavior of a SPA would allot the production of optimal SPAs avoiding a cumbersome trial-and-error approach. Nevertheless, performing FEM analyses of 3D printed soft structures it’s not a trivial task. This study aims at the development of a FEM model to simulate a generic 3D printed bellow SPA performing a pure planar bending motion under pressurization that can be used with different SPA design parameters. The obtained model is used to evaluate properties like the bending angle and exerted forces given a certain combination of design parameters. The performances of a bellow SPA are influenced by several factors (main dimensions, material, operating pressure, shape of the chambers, etc.); this study has considered three main contributors to the bending behavior: wall chambers thickness, number of bellow segments and operating pressure. Many configurations were printed in TPU using FFF printer and tested using a physical rig that measures the bending angle of the actuator and the generated forces. FEM analyses were carried out within Ansys 2019 using a static structural analysis with the actuator fixed at one extremity and pressurized internal surfaces. As hyper-elastic material, Mooney-Rivlin 5-parameters model was used, according to [1]. Material parameters were identified for a limited number of configurations, due to high computational costs, through an optimization process that minimized the bending angle error with respect to actual values. Other actuator configurations were simulated using various sets of parameters derived from the optimization stage and confronted with the physical test results. Results show a valid approximation obtained across the different configurations of the actuators; insights on plausible material parameters for generic 3D printed bellow SPAs were identified. In conclusion, the study has allowed the development of an effective methodology to simulate the behaviour of a generic 3D printed TPU bellow SPA with satisfying level of approximation.