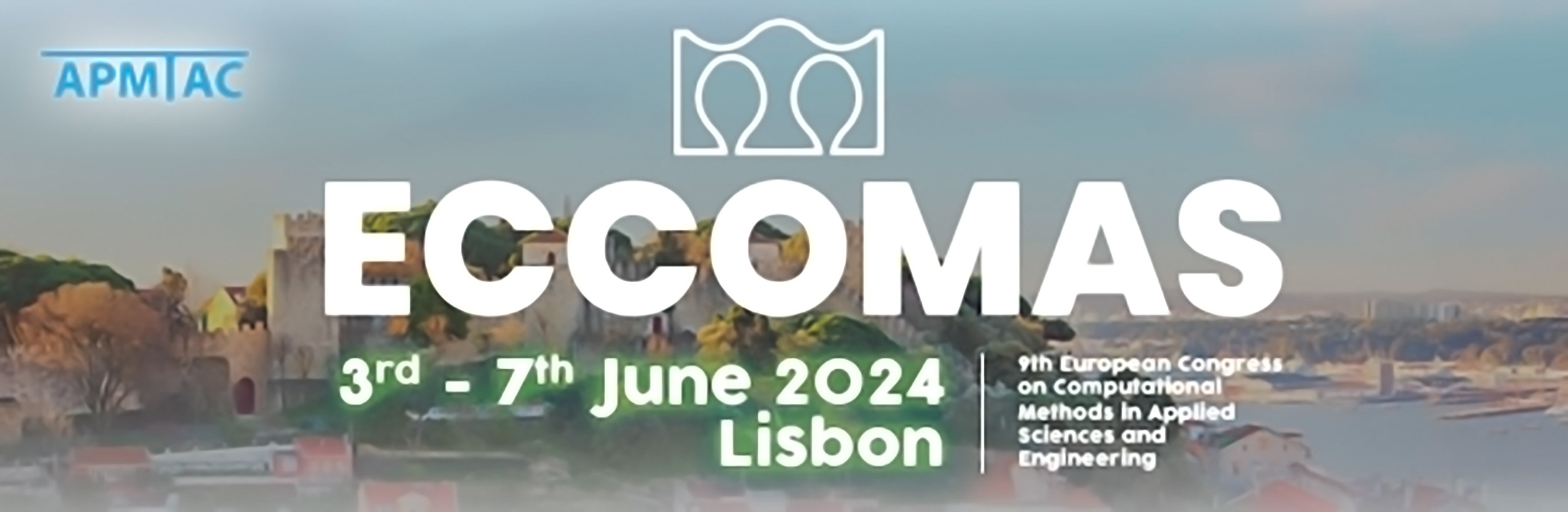
Data driven multiscale modeling of lattice materials: assessment of uncertainties related to manufacturing defects
Please login to view abstract download link
Kirchdoerfer [2] proposed a new approach which avoids the need of constitutive model in computational mechanics, replacing it by material data. In this model free approach, the compatibility and equilibrium equations are kept, while the material model is replaced by the material database made of a number of stress-strain pairs. Material data can be collected either through experimental measurements [1] or numerical simulation. The later is related to recently proposed multiscale data-driven (MSDD) method [4] which permits to generate the material data directly from the lower-scale simulations. As in the standard multiscale (FE^2 ) method, the representative volume element (RVE) with a fine discretization is accurately describing the material microstructure. The advantage of the MSDD method is that the microscale simulation is performed in the offline phase, decoupling this way macro- and microscale. For the (offline) generation of the material database, RVEs are submitted to numerous deformation states enforced with periodic boundary conditions. Using standard computational homogenization enables to constitute the material database containing homogenized macroscopic stresses and strains. In the offline phase tremendous online computations of the classical FE 2 method are replaced by searching points in the database. We explore in this work MSDD method to generate material database which is further used to simulate the deformation process of the metal lattice-based materials [3] produced with Selective Laser Melting (SLM) device. Moreover, the defects inherent to SLM manufacturing lead to uncertainties in the mechanical behavior. To evaluate them, digital twins of manufactured samples serve as RVEs on a cell scale. Taking these uncertainties into account in the material database makes it possible to evaluate a relevant maximum density, which limits computational costs without loss of precision. REFERENCES [1] Leygue, Seghir, Réthoré, Coret, Verron and Stainier, Non-Parametric Material State Field Extraction from Full Field Measurements, Comput. Mech. 64, (2019): 501–9 [2] Kirchdoerfer and Ortiz, Data-Driven Computational Mechanics, Comput. Methods Appl. Mech. Engrg. 304 (2016) 81–101. [3] Liu, Kamm, Garcia-Moreno, Banhart and Pasini, Elastic and failure response of imperfect three-dimensional metallic lattices: the role of geometric defects inducedby Selective Laser Melting, J. Mech. Phys. Solids 107 (2017) 160–184 [4] Karapiperis, Stainier, Ortiz and And