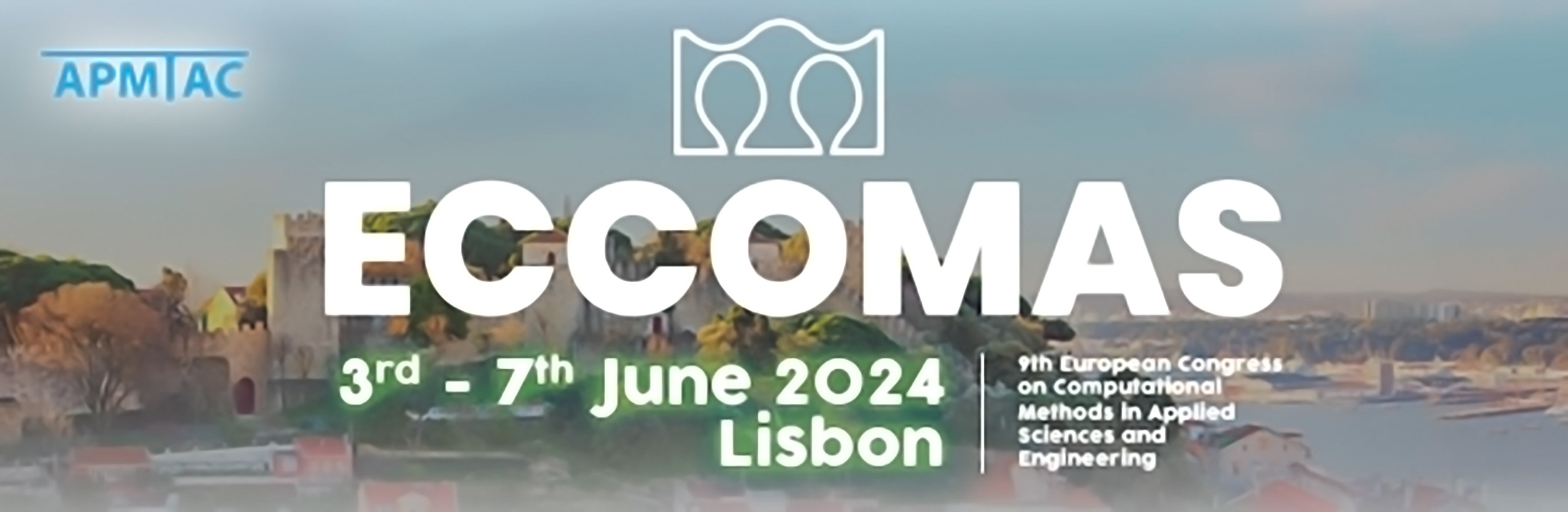
Modeling of Pharmaceutical Agitated Filter Drying: DEM Simulations of Particle Mixing and Heat Transfer
Please login to view abstract download link
The drying of the active pharmaceutical ingredient (API) is an essential unit operation in the manufacturing of pharmaceuticals. Based on API Critical Quality Attributes (CQAs) one would like to achieve a specified moisture (or solvent) content of the API while maintaining the shape and size of API crystals. Agitated filter dryers (AFDs) are commonly used for drying of the API as they allow for the filtration and drying to take place in the same unit, thus reducing the potential for worker exposure to the API powder. During the drying operation, wet API crystals are heated under a vacuum with mechanical agitation to promote heat transfer and solvent evaporation. The temperature of the vessel is constrained by the chemical stability of the API which often leads to long drying times. The agitation rate of the impeller can have a significant impact on drying and insufficient agitation can lead to local hot spots and non-uniform drying, while over mixing can lead to particle breakage and/or agglomeration. The size of the API crystals is a CQA as large particles may have insufficient bioavailability and small particles can cause flow problems and dusting. Intermittent mixing, alternating agitation and no agitation, is a way to achieve a high drying rate while minimizing particle breakage in an AFD process. Here, we focus on Discrete Element Method (DEM) simulations of flow and heat transfer in AFDs. We have carried out simulations to investigate how the impeller speed and extent of intermittent mixing influences the rate and the uniformity of heat transfer. The results show that increasing the agitation rate improves heat transfer up until a critical agitation rate where the rate of heat transfer plateaus. Using dimensionless analysis, we are able to collapse the results into different heating regimes. For intermittent mixing our simulations provide insight into how to distribute mixing across the whole processing time for AFDs. The results have been validated using infrared thermal imaging of a laboratory-scale agitated dryer. Finally, we discuss the implications of these results for the design of mixing protocols for drying and how the protocols impact CQAs.