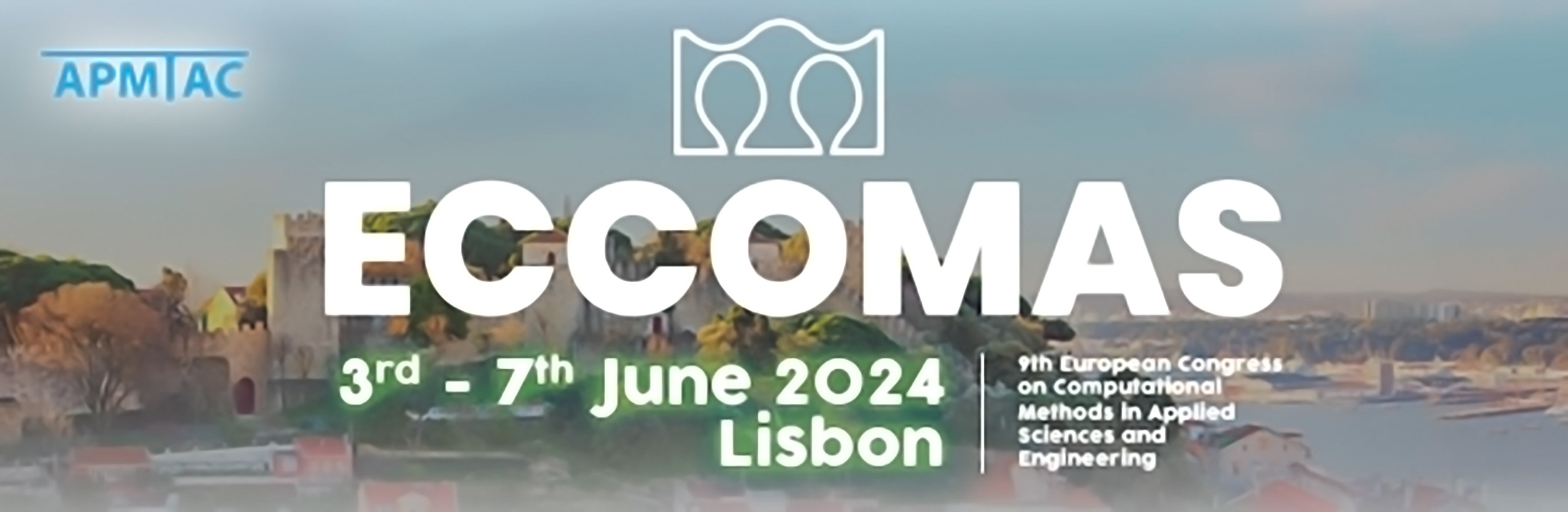
Numerical Simulation of the Multi-Strand Deposition in Fused Deposition Modeling
Please login to view abstract download link
A numerical study of the multi-strand deposition in a fused deposition modeling (FDM) process is carried out in this work. The FDM process is a popular fabrication process mainly used in manufacturing functional parts and rapid prototyping. The numerical framework is based on the stabilized finite-element method and the arbitrary Eulerian-Langrangian (ALE) formulation. Furthermore, a boundary-conforming free-surface approach is used to track the filament motion, allowing an accurate description of the strand shape [1]. The mesh motion is enhanced by using the surface-reconstruction virtual-region method (SR-VR) [2], which is designed for problems with large mesh translation and topology changes, such as the FDM. The Cross-WLF viscosity model is used to represent the shear thinning and the temperature-dependent behavior of the polymer material. The multi-strand deposition is performed by simulating single strands in sequence. A spline-based representation of the shape of previously printed strands is used to include their effect on the current filament simulation. Then, we quantify the interfilament voids remaining after every deposition in the simulated mesostructure. Such voids are later responsible for the porosity of the final object. In an FDM process, it is crucial to accurately predict a quantity like porosity since it directly impacts the mechanical properties of the printed part. Results of the influence of printing parameters on the mesostructure are presented and discussed.