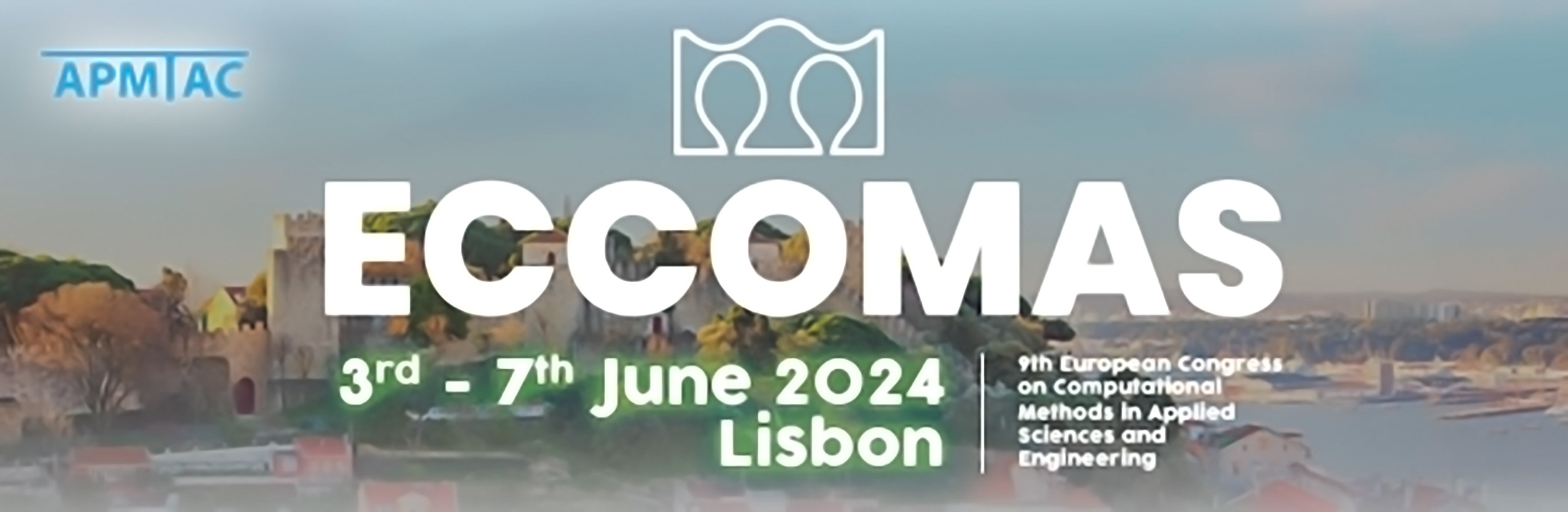
Exploring A Continuous Film Coating Proces with Advanced Simulations
Please login to view abstract download link
Continuous manufacturing is gaining traction in the pharmaceutical industry for its potential to enhance product quality, production flexibility and speed-up the drug production-to-shelf path. Continuous manufacturing offers several key benefits compared to batch production, including decreased downtimes, more compact footprints, and enhanced control over product quality. In this work a continuous film coater (CFC) that employs a unique process design with high rotation rates compared to traditional drum batch coaters is studied. The discrete element method (DEM) and computational fluid dynamics (CFD) are employed for a mechanistic understanding of the coating process. This study utilizes CFD-DEM simulations to delve into the CFC tablet coater through a multi-variant design analysis. The investigation focuses on the thermodynamic behavior of the system as well as the coating mass distribution. The objective is to provide a comprehensive overview of how varying process and material input parameters impact process output responses. The study explores how drying air flow rate, spray rate, and inlet temperature affect coating quality, monitored through tablet temperature and wetness. It also shows how the coating mass distribution evolves over time and how different process conditions impact the final coating mass distribution. Importantly, the simulations demonstrate the capability to numerically recreate the entire coating process, offering a resource-efficient alternative to traditional material and equipment-intensive process development approaches.