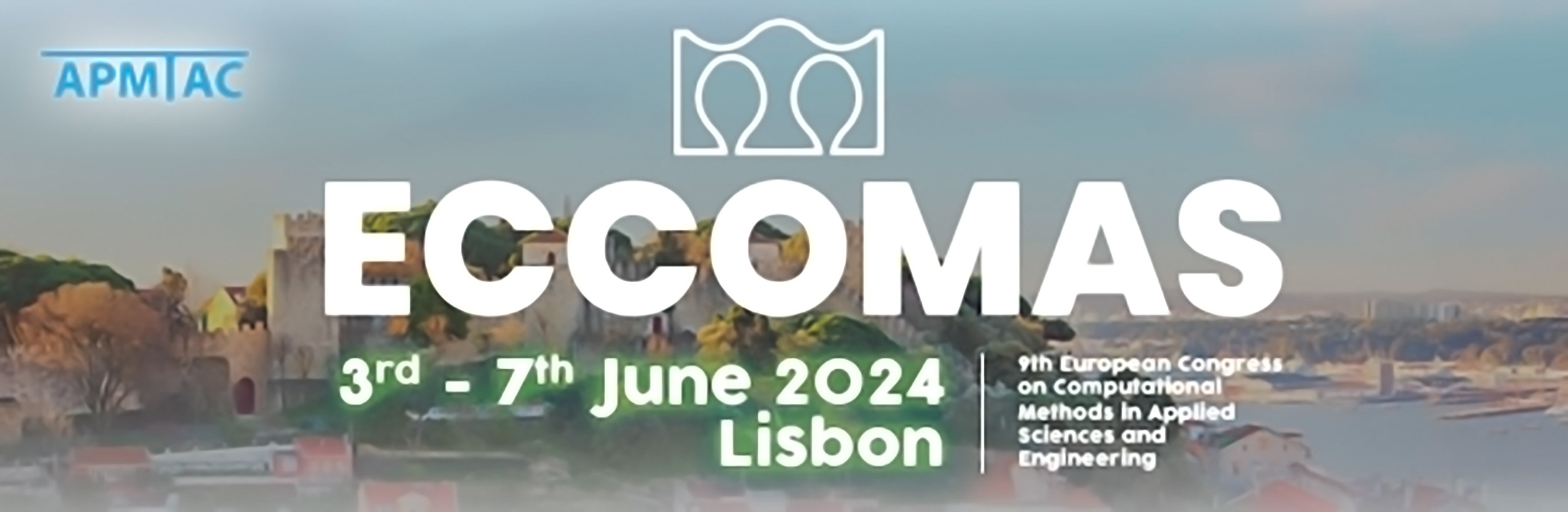
Numerical Simulation of Fluid Flow and Track Formation in a WLAM Process
Please login to view abstract download link
The Wire Laser Additive Manufacturing (WLAM) is an original process developed in the early 1990s. This latter is based on the use of a metal filler wire as feedstock [1] together with a laser heat source dedicated to melting this wire. The bead is then progressively deposited to manufacture the parts of interest. The 3D path of the laser and the metal source define consequently the final geometry of these parts. In WLAM process, the wire was configured initially to be inserted laterally into the melt pool, leading to some clear limitations. In a recent technological breakthrough [2], it has been proposed to introduce the filler wire at the center of several laser beams, regularly distributed and surrounding the metal feeding. This evolution leads to major changes in models dedicated to simulating WLAM processes as energy transportation. In this work, we propose an original method to model heat and fluid flow evolution in a 3-beam WLAM process. The tracking of the metal free interface and the metal bead is achieved in the framework of a level-set approach. Heat and momentum conservation equations are solved by an in-house parallelized finite element software with mesh adaptation. Four single-track deposits are simulated using a representative set of recently published WLAM process parameters [2]. The predicted bead shape morphologies are compared with their corresponding experimental results, demonstrating the efficiency of our methodology. Prediction of the microstructure is also developed and evaluated with the metallurgical analysis performed on the same experimental parts.