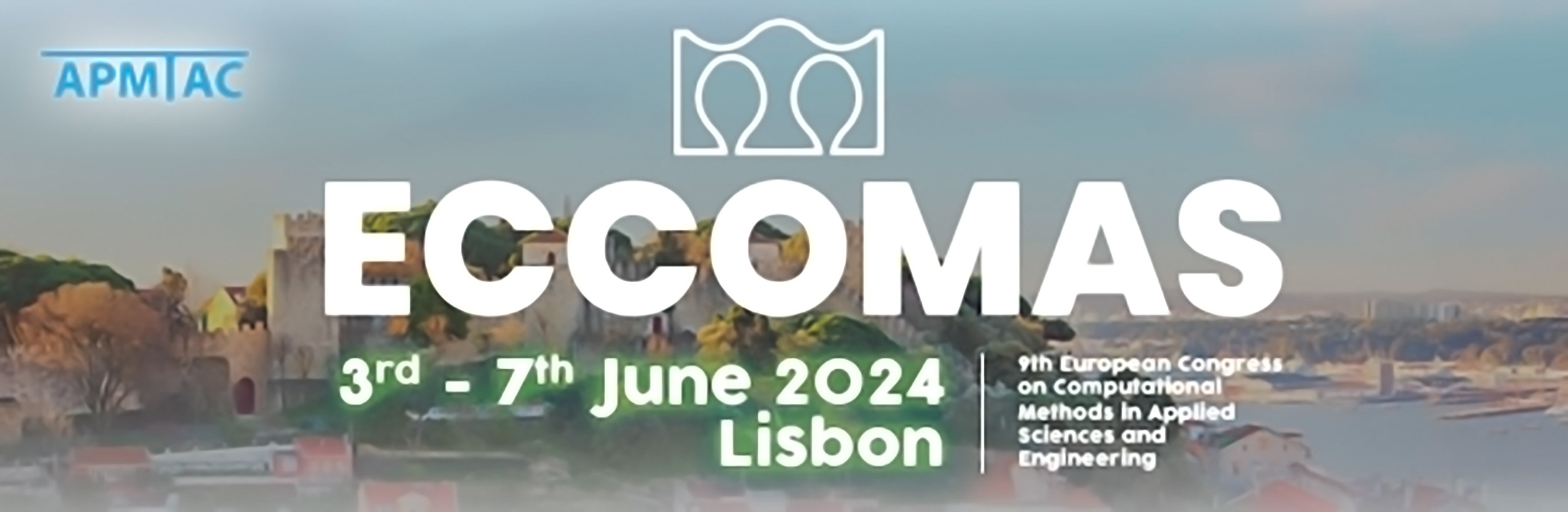
Topology optimization of supports for metal powder bed additive manufacturing
Please login to view abstract download link
This contribution focuses on the design of supports for manufacturing a metallic aircraft component, in the context of metal powder bed additive manufacturing process. In this study supports are needed to sustain large overhanged regions of the part and to mitigate the thermal deformations generated during the printing process. Moreover, a lightweight part/support assembly is a crucial requirement. The design problem is casted as a standard mininum compliance topology optimization problem with a prescribed volume fraction, using two different load models. The first one consists in applying constant loads oriented along the printing direction on detected overhang surfaces of the fixed part. A second strategy consists in applying equivalent thermal loads arising from the layer by layer simulation printing process [1]. Optimized supports using (a combination of) both models will be presented and discussed. The proposed approach relies on a simplified model of the process simulation and is compatible with the overall cost of the optimization process, paving the way for setting up a Design of Experiments and further validation through detailed FEM analysis. The numerical implementation has been developed using the Research and Development open source software OpenPISCO [2]. The numerical optimization strategy relies on the level set method, the notion of Hadamard shape derivative linked to the computation of an advection velocity and a null space algorithm to handle constrained problems [3].