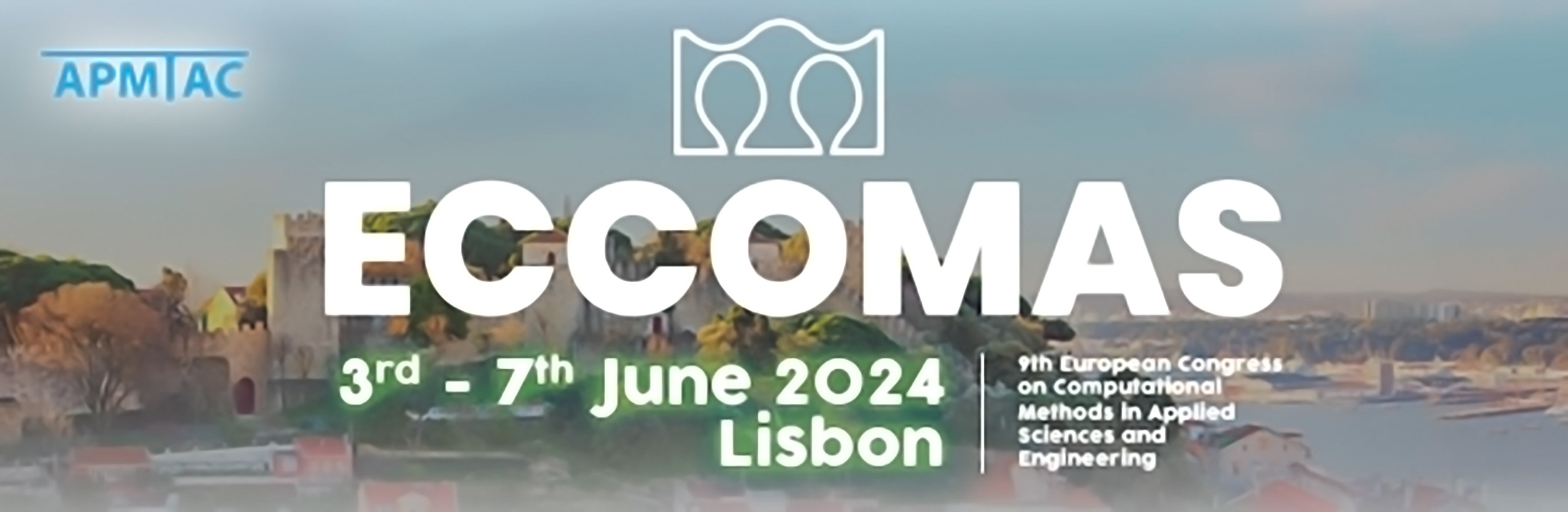
Multi-Phase-Field Modelling for AM Processes Simulation Including In-Situ Thermal Fracturing
Please login to view abstract download link
In the field of engineering, addressing the intricate challenges of thermal fractures in metal additive manufacturing poses a significant task. This study leverages the power of parallel modeling and the Multi-App feature in MOOSE to present a comprehensive solution to this complex issue. Our approach involves coordinating both the Main-App and sub-applications to explore the subtleties of thermal fracture modeling. The Main-App is dedicated to simulating the underlying physics, covering processes such as heating, phase change from powder to liquid state, and solidification. This is accomplished using the Allen-Cahn phase field, coupled with an elastoplastic model, all facilitated by the Multi-physics Object-Oriented Simulation Environment (MOOSE). Subsequently, this data seamlessly transitions to the sub-application for a meticulous analysis of thermal fractures. The sub-application is specifically designed to focus on modeling liquation cracks in Inconel super alloy, utilizing diffusive phase field crack modeling with an additional energy scale of Allen-Cahn to control non-conserved damage evolution. Efficiency and computational time optimization are achieved through the implementation of a staggered method for process synchronization, ensuring the seamless exchange of data between the Main-App and sub-application. Additionally, we employ an adaptive mesh to finely control the interface, guaranteeing precise and accurate modeling of thermal fracture dynamics. Our findings shed light on the impact of process parameters in additive manufacturing and their complex multiscale intrinsic nature, aiming to identify optimal conditions and minimize imperfections.