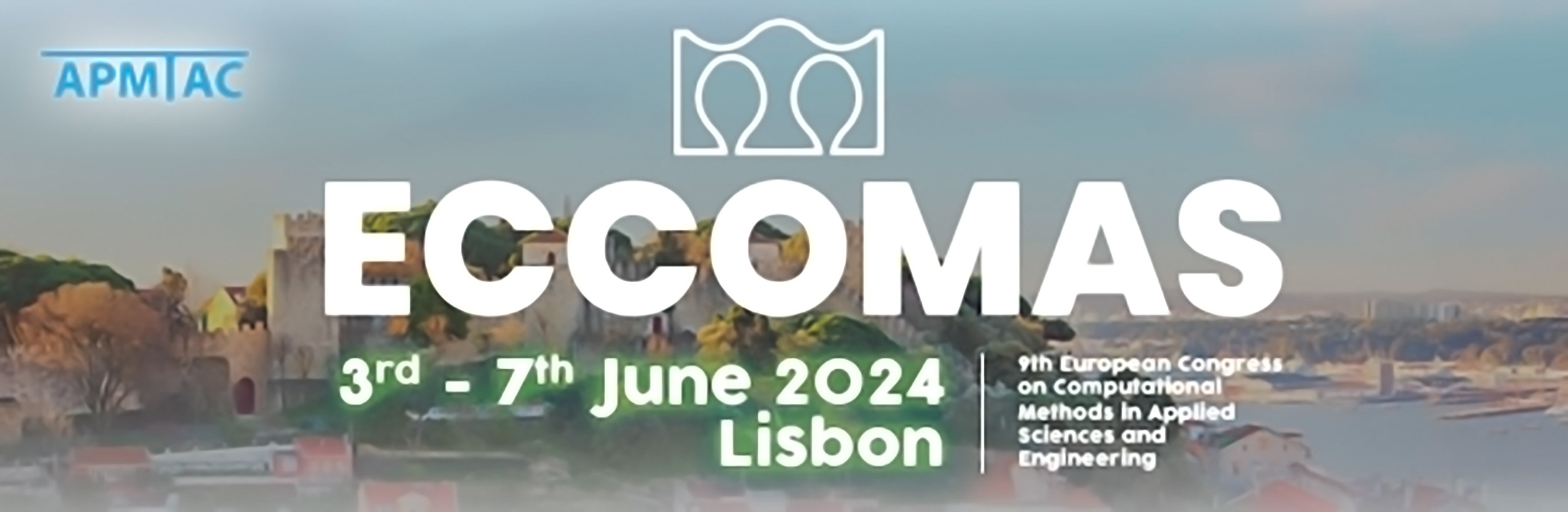
Fast Thermal History Prediction During Additive Manufacturing Processes Using Deep Learning Methodologies
Please login to view abstract download link
Despite the technological progress that has been made in Additive Manufacturing (AM) over the past decade, there are still significant scientific research and challenges that need to be addressed to advance AM towards a reliable manufacturing process and a widespread adoption in the industry. AM involves numerous and complex parameters to be monitored and controlled during the process to achieve an acceptable level of accuracy. In this context, Artificial Intelligence (AI), and in particular Machine Learning (ML), methods can be applied in various aspects of AM, such as design for AM, process parameter selection, process and performance optimization, in-situ process monitoring and control, real-time anomaly detection, post-process monitoring and control, etc… to improve the whole design and manufacturing workflow. Our current challenge is focused on the development of advanced AI-based tools and methodologies dedicated to temperature field and history prediction at the scale of the manufactured part, first step for a better AM process optimisation and control. This model is addressed to provide a much faster temperature history compared to classical finite element models but still accurate. For this sake we leveraged advanced deep learning techniques. Our metamodels rely on Graph Neural Networks (GNN) and Recurrent Neural Network (RNN) to predict the temperature history for a variety of process parameters and part geometries. GNN are particularly suited to represent physical fields defined on a complex mesh, such as temperature on a part geometry. Making a stable and accurate prediction of a physical field over a long period of time is also a challenge. We are currently developing specific hybrid RNN GNN models and testing some alternative models to achieve these objectives. As part of our initial work, the training data sets are carried by an AM numerical model. Different types of databases have been generated by increasing the complexity of a 2D numerical modelling, starting from a dataset based on the simulation of a simple wall part manufacturing with a fixed geometry and going to a database which clustered wall part manufacturing simulations with a variety of complex geometries.