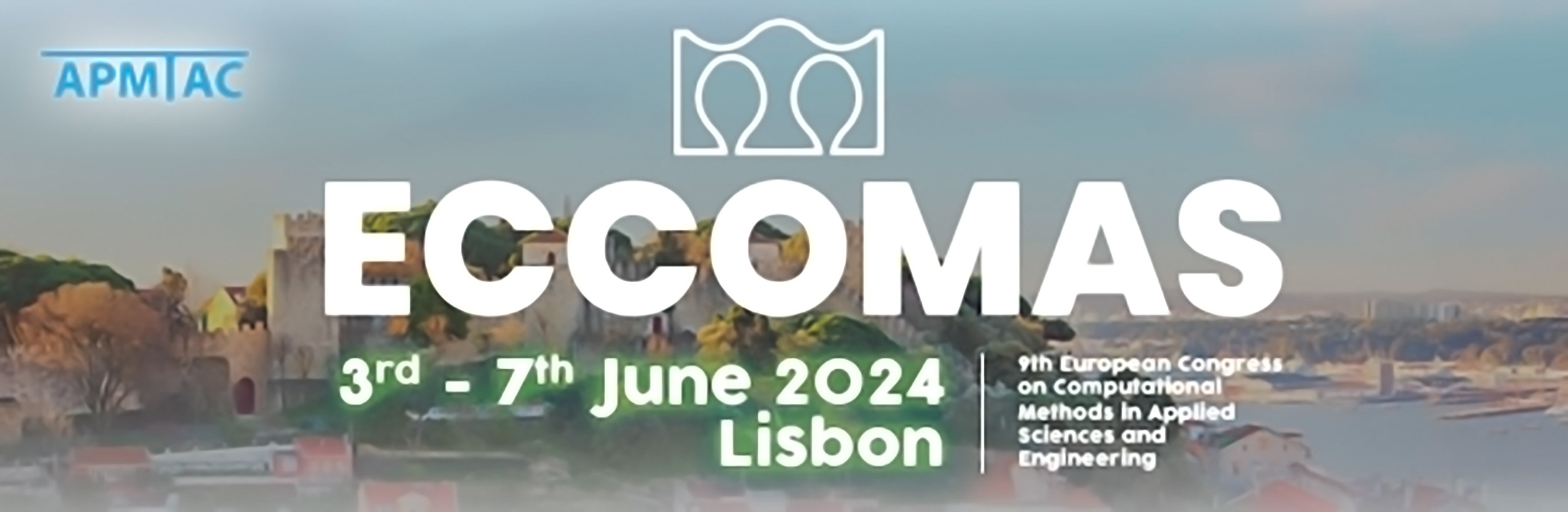
Development of a Simplified Model for the Analysis of Bolted Assemblies under Extreme Loadings
Please login to view abstract download link
Bolted joints are very common in mechanical engineering, particularly in aeronautics (for example, 3,000,000 joints on an A380). Their optimization requires elaborate design strategies that take into account the various phenomena involved in assemblies, such as contact, friction and plasticity. These optimizations cannot be carried out efficiently using 3D models, due to the prohibitive computational costs involved. Although various simplified finite element models are generally available in commercial finite element software, they often have limitations (linear elastic behaviour) or require substantial resources to implement [1,2]. This work proposes an extension of the model developed in [3] in order to represent the whole behaviour, in particular, the macro-slip under the head (or under the nut) as well as the contact between the screw body and the bore. This approach aims to reduce computational costs, while maintaining an adequate level of representation of the macroscopic quantities of interest (sliding, Von Mises stresses). On the basis of design parameters (bolt preload, friction coefficient, bolt dimensions), the current connector is implemented as a user element in Abaqus/Standard. Comparative analyses will be presented, contrasting fine-scale 3D calculations with simulations employing connectors in bolted assemblies. REFERENCES [1] P.J. Gray, C.T. McCarthy, A global bolted joint model for finite element analysis of load distributions in multi-bolt composite joints, Composites Part B: Engineering, Vol. 41, Issue 4, 2010. [2] Jeong Kim, Joo-Cheol Yoon, Beom-Soo Kang, Finite element analysis and modeling of structure with bolted joints, Applied Mathematical Modelling, Vol. 31, Issue 5, 2007. [3] R. Verwaerde, P.-A. Guidault, P.-A. Boucard. A non-linear finite element connector model with friction and plasticity for the simulation of bolted assemblies, Finite Elements in Analysis and Design, Vol. 195, 2021.