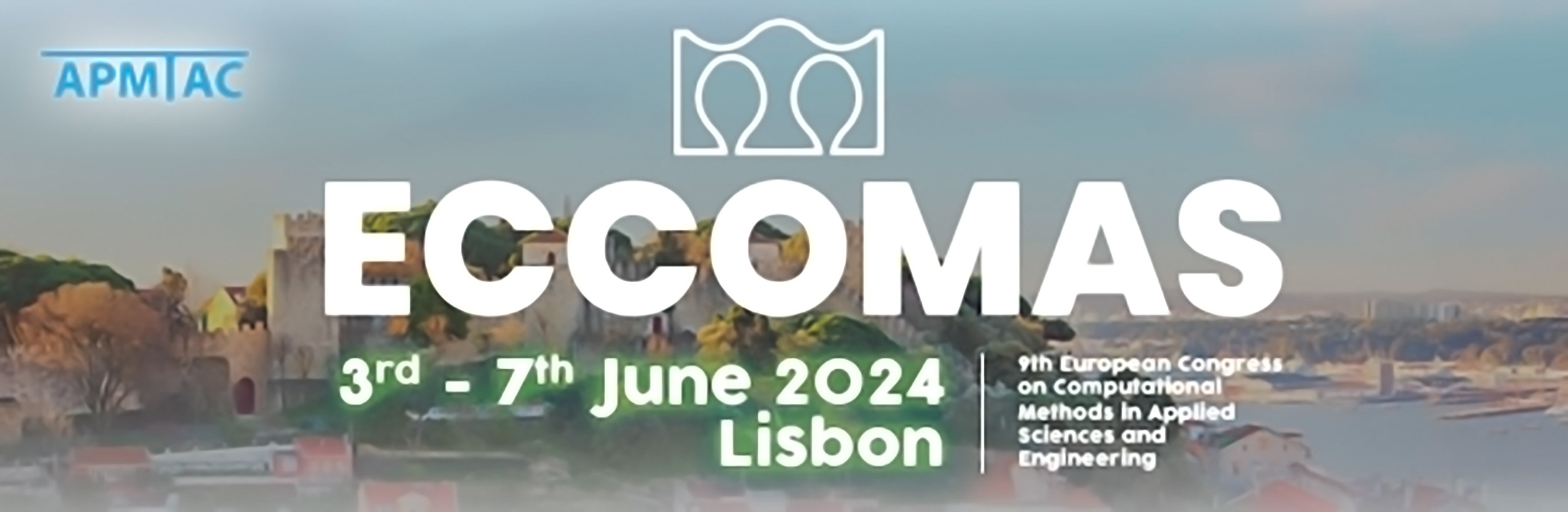
Fluid-Structure Interaction Framework for the Design of Extrusion Dies using the Immersed Boundary Surface Method in foam-extend
Please login to view abstract download link
In the extrusion of plastics, the down time of extrusion lines is partly due to thermal inertia of the voluminous components. At the same time, extrusion dies are often over-designed. Different lightweight strategies, such as reducing the excess volume and mass brought on by over-design, are investigated using simulations to minimise thermal inertia while maintaining structural integrity. To achieve this goal, the simulation environment must capture the fluid-structure interactions (FSI) between the plastic melt flow in the die and the flow-dependent deflection of the die plates, as well as allow the die geometry to be automatically adjusted. Both challenges can be met by using the immersed boundary surface (IBS) method, which has barely been established in plastics processing so far. The IBS method as implemented in the OpenFOAM extension foam-extend-5.0 follows a cut-cell approach, while allowing for accurate boundary representation on the calculated virtual interface. The main advantage of this method is its flexibility as it allows for a partitioned coupling approach for the FSI simulation without the need to re-mesh either of the geometries during runtime. Due to the polymer's high fluid density and viscosity, the interface coupling between melt and die poses a numerical challenge, and there is no established ideal coupling strategy for this application. Different coupling strategies are investigated for the interaction between melt flow and the extrusion die. The results outline general recommendations regarding the coupling for FSI applications in plastics processing.