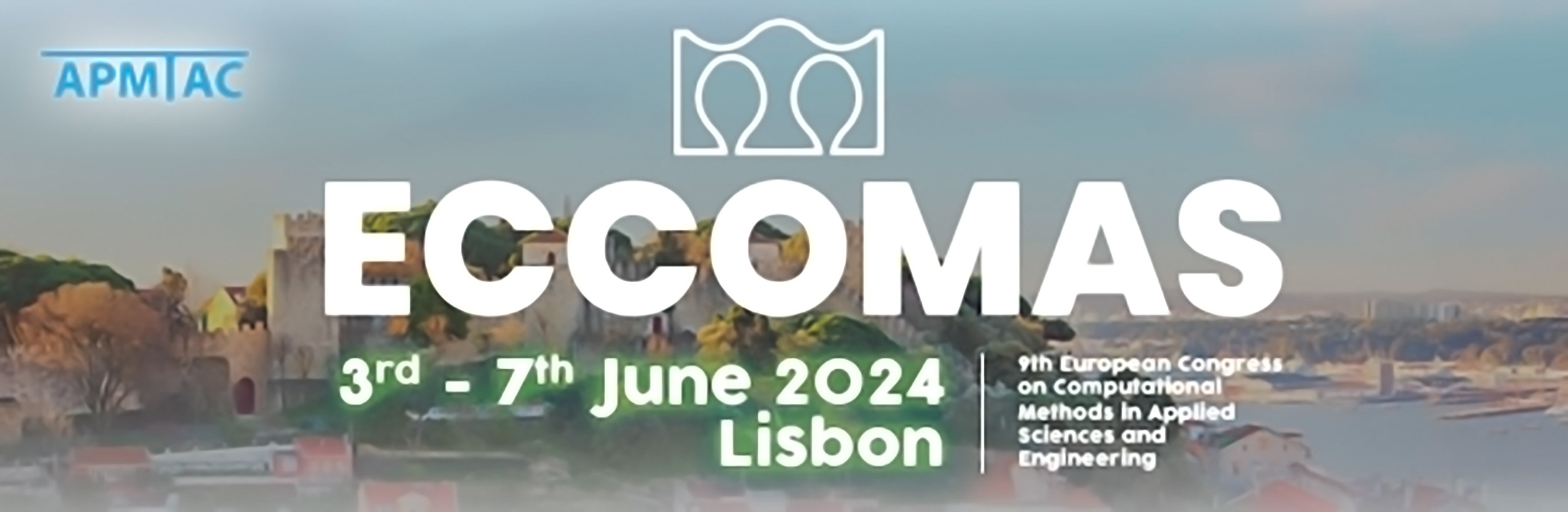
A phase transformation model for multiphase alloys applied to laser powder bed fusion processes
Please login to view abstract download link
Titan aluminium alloys, categorised as multiphase α-β-alloys, find extensive application in various industrial settings due to their favorable mechanical properties. However, the material properties are significantly influenced by the composition of their crystal structure and the corresponding solid fraction. The thermal history, specifically the cooling rate, determines the phase composition and microstructure, particularly in processes with high temperature input, for example heat treatment and additive manufacturing processes. The modeling and simulation of, e.g., laser powder bed fusion (LPBF) processes requires careful consideration of transitions between melt, β- and various α-phases for reliable results. Numerous modeling approaches are available in literature, mostly relying on algebraic equations under isothermal conditions based on the Johnson-Mehl-Avrami-Kolmogorov (JMAK) theory and the Koistinen-Marburger (KM) model. The present contribution introduces a melt-solid-solid phase transformation framework based on energy densities and thermomechanically fully coupled evolution equations. This ansatz effectively captures the divers material compositions resulting from varying cooling and heating rates. The modelling approach can straightforwardly be extended so as to incorporate additional phase fractions and different materials. In contrast to empirical formulations, the developed model is both, thermodynamically consistent and physically sound. Particularly the evolution of the underlying phases is governed by a specifically designed dissipation function. The coefficients of the extended dissipation function are determined through a parameter identification by using a limited number of experiments or continuous cooling temperature (CCT) diagrams from the literature. This enables the prediction of a model-based CCT diagram that consistently aligns with existing literature data. This formulation facilitates the prediction of microstructure evolution not only on processes characterised by high temperature gradients, as seen in LPBF processes, but also provides insight into the evolving strains and stresses throughout and at the end of the process. Temperature profiles taken from process-based LPBF simulations illustrate the model’s capabilities. The associated temperature profiles exhibit significant heterogeneity in both space and time, adding to the overall complexity.