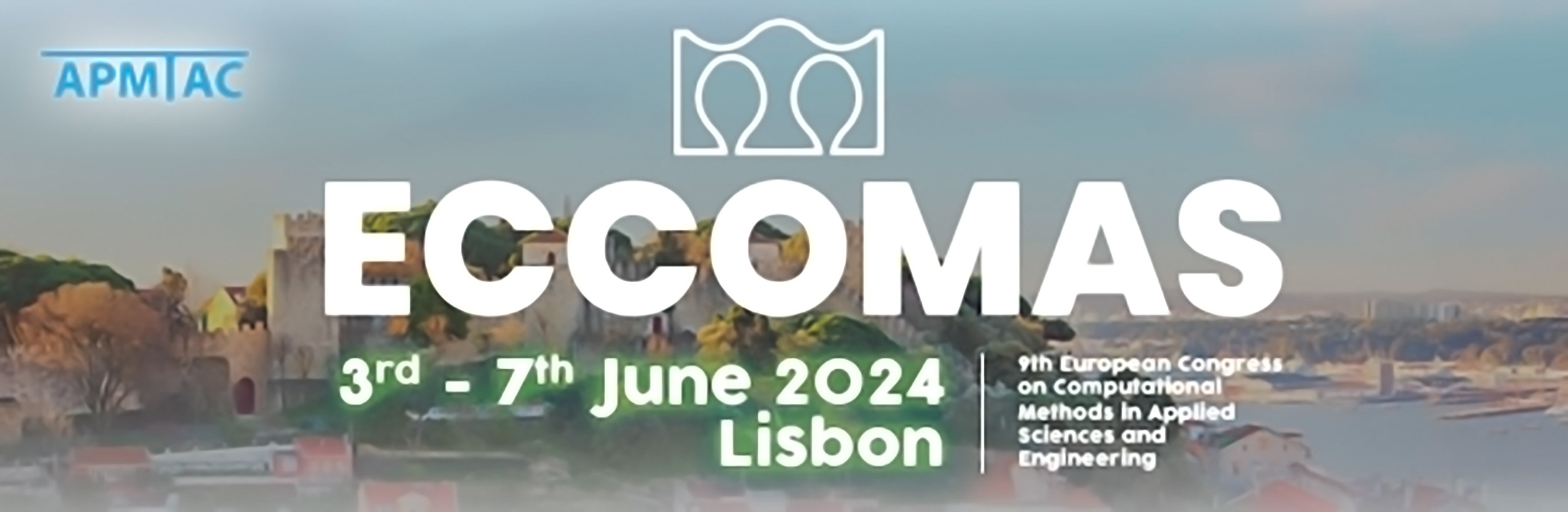
Non-intrusive Inference of Digital Twins from Multi-physical Simulation Data of Additive Manufacturing Processes
Please login to view abstract download link
A digital twin is a virtual representation that accurately replicates its physical counterpart, fostering bi-directional real-time data exchange throughout the entire process lifecycle. This study explores the integration of digital twins into additive manufacturing processes, particularly focusing on lattice structures. In additive manufacturing, digital twins help to control the process better and progressively react to unplanned processing results. Employing faster-than-real-time and highly accurate surrogate models enables the prediction of altered structural properties, facilitating on-the-fly re-optimizing the ongoing manufacturing process to still achieve desired structural outcomes. Consequently, this approach contributes significantly to realizing the first-time-right paradigm in additive manufacturing. The foundation of successful digital twin derivation lies in the physics-based modeling of the additive manufacturing process. Predicting final structural properties necessitates mapping input parameters to potentially non-linear material properties [2]. However, a challenge arises from the need to provide faster-than-real-time replications of these mappings through simulations, particularly as the complexity and computational cost of multi-physical simulation models increase. This study addresses the aforementioned challenge by presenting an efficient training methodology for digital twins, utilizing only minimal training datasets extracted from multi-physical simulation models. An efficient design of experiments aids in selecting representative training data, ensuring minimal test error on the twin when applied to pertinent test data. The proposed solution includes a comprehensive software suite that automates simulation model management, training data selection, reduced-order model derivation, and integration of digital-twin-based control techniques into a unified framework. The versatility of this framework, specifically designed for seamless integration with various simulation models, was initially exemplified through its application in autonomous thermal food processing [1]. Remarkable efficiency gains are achieved. Computational efficiency is demonstrated by characteristic solution times of one-tenth of a second, imposing negligible processing costs on a single-core processor. The framework showcases practical viability by predicting field data with 4649 spatial points and one hour of real-time processing outputs within less than 0.5 s.