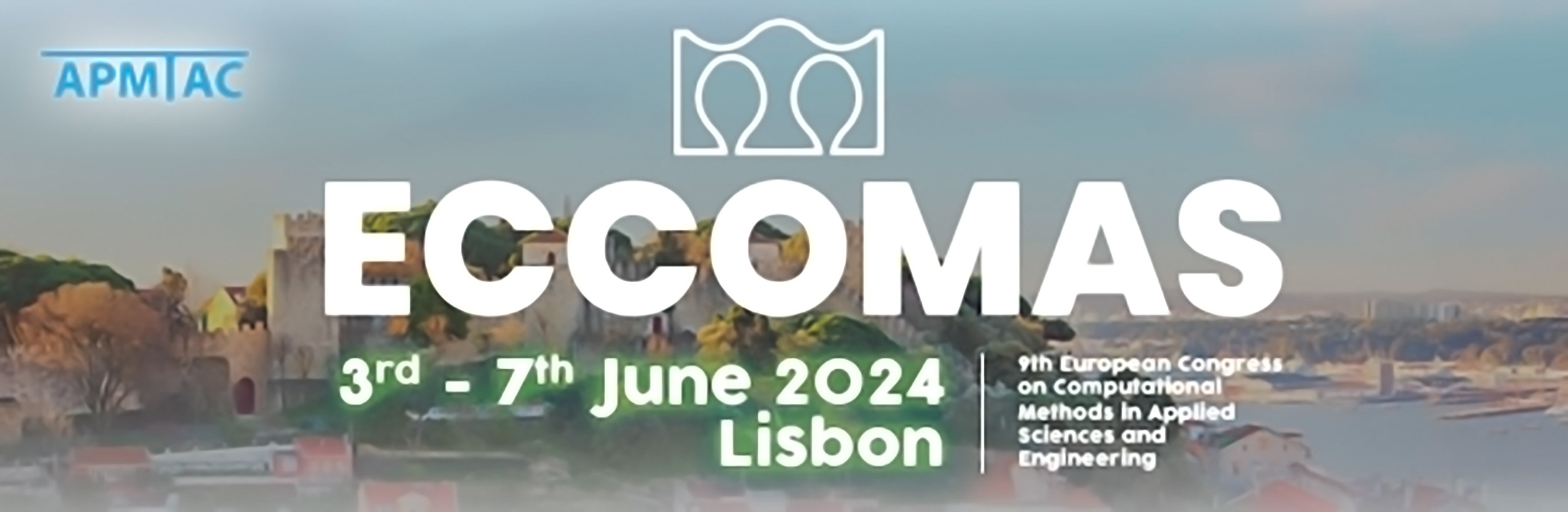
Investigating cold compaction of Al-TiB2 and Al-SiC powder mixtures using finite element modeling validated by compaction experiments
Please login to view abstract download link
In recent decades, composite materials based on a metallic matrix reinforced with ceramic particles have replaced traditional monolithic alloys in many applications in the aerospace, automobile, and nuclear industries. These composites offer the potential of enhanced thermal and mechanical properties and greater durability in service. An attractive method for fabrication of metal-ceramic composites is the use of cold compaction of a metal-ceramic powder mixture followed by sintering at high temperatures. During the compaction stage, the time dependent hydrostatic stress at each material point, governs the final density distribution of the component. Large density gradients can result in defective components with low thermal conductivity and reduced ductility and strength. As a consequence, predicting the density distribution during the compaction stage is critical. Although many analytical models can provide average values of the compact density, due to the complex non-linear nature of the compaction process, numerical methods must be utilized to obtain local values of density. This research focused on investigating the cold compaction process of Al-TiB2 and Al-SiC powder mixtures (0-15% volume fraction of TiB2 and SiC in the Al were considered) using finite element analysis in conjunction with compaction experiments. The powder mixture was assumed to behave like a porous media and was modeled using the Gurson-Tvergaard-Needleman (GTN) approach. A density dependent elastic response of the powder mixture was also incorporated using a user defined sub-routine in the commercial code ABAQUS. Convergence studies were used for solution verification and compaction experiments were used to both identify the GTN model parameters and to validate to computational models. By comparing the computations to the compaction experiments, it is demonstrated that a density dependent elastic response is required in order for the GTN model to accurately represent the observed initial part of the compaction curve where the relative density is low. The study also reveals that the GTN model parameters q1 and q2 can be correlated to the volume fraction of the ceramic reinforcement particles. From a practical point of view it is also shown that increasing the volume fraction of the ceramic reinforcement, although increasing initial powder density results in greater local density gradients.